What is Zinc Die Casting Mold?
Zinc alloy die casting mold is suitable for the zinc alloy die casting process.
After the zinc alloy is melted, the hot chamber die-casting machine injects the high-temperature zinc alloy liquid into the steel mold at high speed through the piston, makes it cool and solidify in the mold, and finally obtains parts or components that meet the requirements in shape and size.
Because the die-casting temperature of zinc alloy is much lower than that of aluminum alloy and brass alloy. Therefore, the requirements for mold steel are not high. Usually, ordinary hot work die steel is fine. To increase the lifetime of zinc alloy die-casting molds, it is necessary to improve the wear resistance and hardness of the mold. We use H13-type hot die steel, high-temperature quenching, high-temperature tempering, and the hardness is generally around HRC50. Cost-effective, and long lifetime.
To further improve the working life of the mold, we can use high-temperature quenching and high-temperature tempering for hot work die steel with a hardness above HRC52, such as LG1.2367, YXR33, 8566X, W360, etc.
The materials above are more expensive, we can also choose good quality H13 as the base material, and improve the wear resistance through surface treatment to achieve the purpose of improving the lifetime of the mold.
Zinc Die Casting Molds Making Process
Zinc alloy has a low melting point, good fluidity, and less impact and wear on the mold. The service life of zinc alloy die-casting molds is generally above 200,000-500,000 shots mold times. A good zinc alloy die-casting mold can reach more than 100w mold times.
However, while considering the number of shots, we also need to consider the price of the mold per unit mold. How much does it cost for the same mold for 500,000 molds? Or even 1000,000 shots?
Yontone as a zinc die casting mold maker, has decades of experience in the design and production of die-casting molds, we will help customers weigh what material to use in this order is the most cost-effective, and supplying guaranteed excellent quality mould is our mission.
The cavity of the zinc alloy die-casting mold is a precision machining task. After processing, the cavity shape is consistent with the mold design drawings. The processed cavity needs to undergo heat treatment to meet the hardness requirements of the zinc alloy die-casting process for the mold.
Utilizing copper or graphite as electrodes, the mold is processed through Electrical Discharge Machining (EDM) on an EDM machine. This method allows for the machining of intricate shapes that are challenging to achieve through traditional mechanical machining methods. Yontone zinc die casting mold offers high precision and an excellent surface finish.
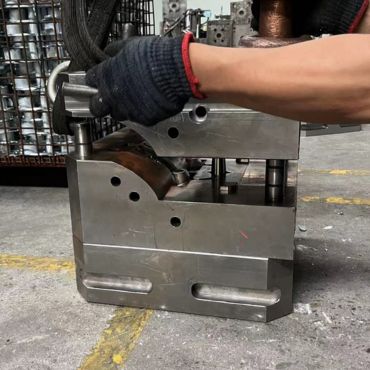
Assemble the core, ejector pin, insert block, slider, top plate, bottom plate, mold frame, mold base, and other components together. Simultaneously, through proper fitting of the mold components, ensure good mold closure, no flash during production, and achieving excellent moldability. Once this is achieved, the zinc die casting mold is ready for production.
Zinc Die Casting Molds
Zinc alloy die-casting products have excellent surface quality, zinc alloy molds are typically employed in the production of intricate shapes for zinc alloy die-castings and have been widely used in the manufacture of toys, tableware, locks, hardware decorations, electrical and electronic castings, faucet body and handles, bathroom accessories, auto parts, marine parts, zippers, metal buckles, watch cases, fans, daily necessities, household appliances, photographic equipment, medical instruments, audio, mechanical and electrical products.
Because most zinc alloy die castings have surface treatment requirements such as post-polishing and electroplating, the requirements for mold precision and surface finish are relatively high.
As a zinc die casting mold company, Yontone supplier customized high quality mold according to client’s product drawing or real samples.
Advantages of Zinc Die Casting Mould
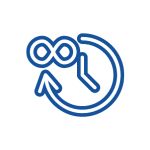
Because the melting point of zinc alloy is low, the service life of zinc alloy die-casting mold is longer than that of aluminum alloy and copper alloy die-casting mold. It is 200,000-500,000 shots mold times. If the maintenance is good, Yontone moulds can produce up to 1000,000 shots.
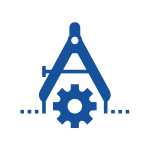
The local dimensional tolerance of zinc alloy die-casting molds can reach 0.02mm, and the thin-walled dimension of zinc alloy die-casting parts can reach a minimum of 0.25mm.
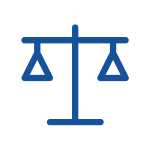
Due to the good fluidity of zinc alloy, zinc alloy die-casting molds can cast die-casting parts with complex shapes, clear outlines, thin walls, and deep cavities.
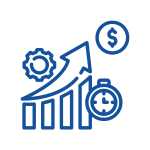
Zinc alloy die-casting mold with high surface finish and easy de-moulding. The die-casting process of zinc alloys is easier to mechanize and automate.
Optimally Structured Zinc Die Casting Mold Design
Yontone’s professional zinc alloy die-casting mold design team will design product molds based on the customer’s existing die casting size, quantity, and annual usage. Ensure that the structure of the mold and mold cavity number can meet the production needs of customers to maximize production efficiency. Simultaneously, utilize mold flow analysis to validate the mold design.
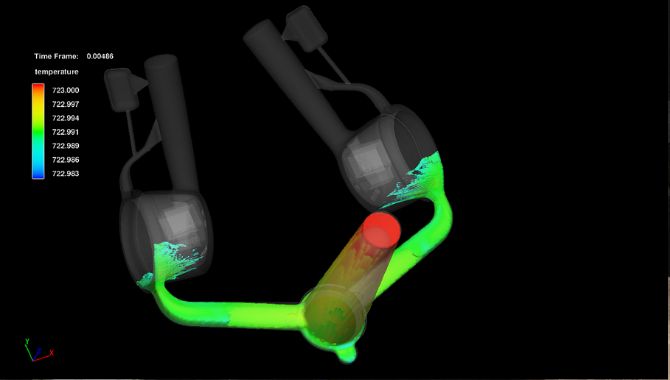
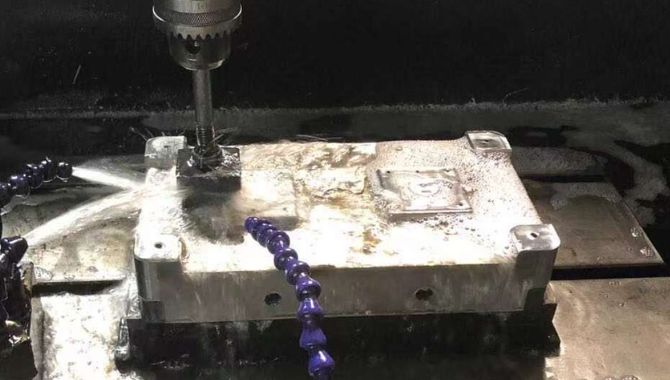
Durable Zinc Die Casting Mold with Long Lifespan
The molds produced by Yontone lifetime can reach 200k – 500k shots, and have the following characteristics.
- good mold design has a reasonable structure, and the metal liquid will not impact the surface of the mold, making it durable and durable.
- good mold materials have toughness and hardness and can accept zinc alloy die-casting with hundreds of thousands of molds.
- the maintenance of the mold and the operation of the die-casting process can also affect the lifespan of the mold.
Enhancing Efficiency with Zinc Alloy Die-Casting
More and more customer companies are now equipped with automatic die casting systems.
As an excellent supplier of zinc alloy die-casting molds, Yontone moulds are reasonably designed and not easy to stick to the mold, suitable for both automatic die casting and manual die casting.
If your factory is equipped with automatic spraying, feeding, and die-casting pick-up arms for zinc alloy hot chamber die-casting machines, our moulds can be greatly improved the production efficiency of your automated die-casting.
Of course, if your company uses manual labor to die-cast zinc alloy products, such high-quality molds will also greatly improve the work efficiency of your workers.

Technical Support for Zinc Alloy Die-Casting Molds & Production Efficiency
For customers who only purchase zinc alloy die-casting molds and make die casting parts in their factory, we will also provide comprehensive technical support for die-casting parameters, provide mould trial data and video, to help customers shorten the debugging time of the die-casting machine and improve the efficiency of the production of bulk goods results in a composite product rate.
Why Choose Yontone As Your Zinc Die Casting Mould Supplier
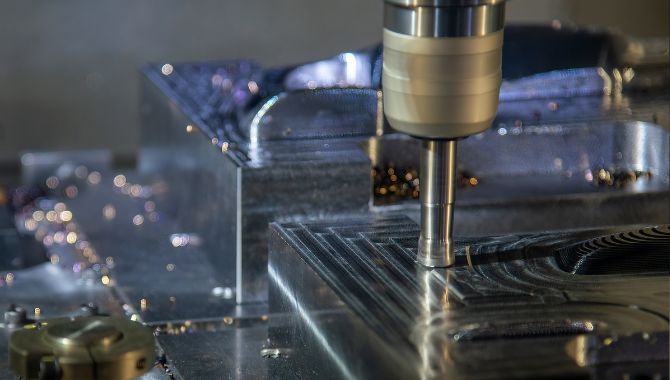
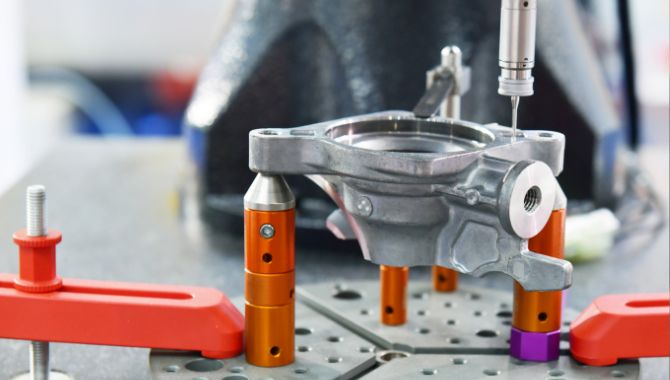
Zinc Alloy Die-Casting Mold Supplier, Design and Expertise at Yontone
- The design of zinc alloy die-casting molds significantly impacts product quality. In the process of designing and manufacturing zinc alloy die-casting molds, improper material selection, design, and construction can lead to increased chances of dimensional inaccuracies and poor product appearance. Therefore, high-quality zinc alloy die-casting molds lay a strong foundation for producing top-quality zinc alloy die-casting components.
- Each metal material has its unique characteristics, and the design of molds for zinc alloy, aluminum alloy, and copper alloy varies significantly. At Yontone, our mold designers have specialized expertise in the field of zinc alloy die-casting, with over 8 years of experience. They are well-versed in the characteristics of zinc alloy and hot chamber die-casting machines. Based on customer requirements, they collaborate with die-casting design engineers and machining engineers to establish dedicated project teams. These teams optimize mold designs and ensure efficient production processes, resulting in high production efficiency and precision for zinc alloy die-casting molds.
- As Yontone is a one-stop supplier for zinc die-casting molds, zinc die-casting, and machining, if customers purchase only zinc alloy die-casting molds from our company, we provide mold trial parameters and optimization suggestions based on the customer’s die-casting machine and actual production conditions. Our production capabilities in zinc alloy die-casting and machining validate the strength of our zinc alloy die-casting mold design and production capabilities.
When purchasing die-casting molds, especially zinc alloy die-casting molds, it is advisable to choose a company like Yontone with extensive experience in zinc alloy die-casting production. This ensures better assistance with operational and setup issues during the die-casting process.
- Competitive Advantage: Yontone’s years of experience in zinc alloy die-casting production have enabled us to discover mold optimization methods. We excel in optimizing runner design to reduce zinc alloy material waste, improving gate and runner design to minimize defects like blemishes and porosity caused by inadequate venting, and ensuring optimal mold design while delivering high-quality products at competitive prices.
- Lead Time: Zinc alloy die-casting products are generally smaller than aluminum alloy die-castings, and zinc alloy die-casting machines are smaller as well. Therefore, the production lead time for zinc alloy die-casting molds is shorter compared to aluminum alloy die-casting molds. Typically, after confirming the mold design drawings, zinc alloy die-casting molds can deliver the first trial samples within 20-40 days. We sign agreements with customers at the time of order placement to establish clear delivery schedules. For urgent orders, we offer expedited services. Rest assured, we always deliver within the promised lead time.
- Vision: As a company with 35 years of mold production and design experience, Yontone aims to be a century-old enterprise and beyond. This vision is built on our dedication to exceptional service, high-quality products, and the trust of our customers. Every zinc alloy die-casting mold that leaves Yontone is produced with utmost care and commitment to excellence.
Wild Application Fields of Zinc Die Casting Molds
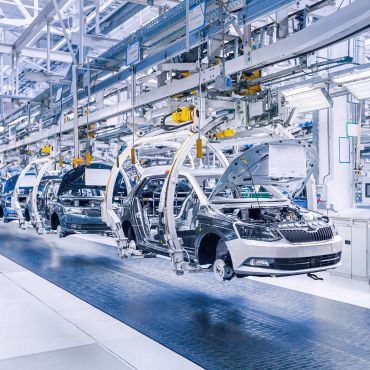
Zinc alloy die casting molds have extensive applications in the automotive industry, including:
- Interior components such as dashboards, steering wheels, and seats.
- Powertrain components such as engine covers, radiators, and fuel tanks.
- Brake system components such as brake discs and calipers.
Zinc alloy products manufactured using molds designed by Yontone exhibit excellent mechanical performance, meeting the requirements for strength, rigidity, and wear resistance in automotive components. They also demonstrate good corrosion resistance, fulfilling the demands for automotive parts used in harsh environments.
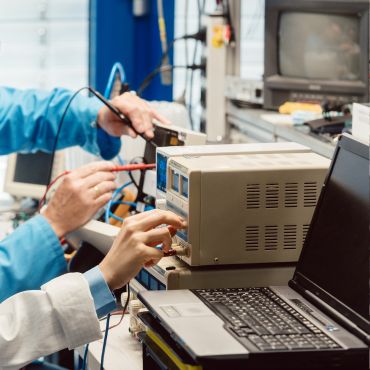
Zinc alloy die casting molds find extensive applications in the electronics and electrical industry, including:
- Casings for electronic products such as computers, mobile phones, and televisions.
- Housings for electronic components like power supplies, switches, and sockets.
- Supports for electronic components like circuit boards and connectors.
- Heat-dissipating components such as radiators and heat sinks for electronic devices.
Zinc alloy die-casting parts produced by Yontone’s molds exhibit excellent conductivity, meeting the electrical conductivity requirements of electronic products. They also demonstrate good corrosion resistance, fulfilling the demands for electronic products used in harsh environments. Additionally, these die-castings possess excellent recyclability, aligning with environmental sustainability requirements.
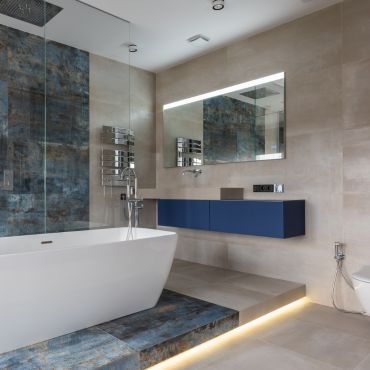
In the home and construction industry, zinc alloy die casting molds find application in:
- Decorative accessories such as door handles, faucets, and lighting fixtures.
- Hardware tools, mechanical components, and other related parts.
Zinc alloy die-castings produced with molds manufactured by Yontone exhibit excellent decorative qualities, meeting the aesthetic requirements of the home and construction industry. Simultaneously, they demonstrate good corrosion resistance, fulfilling the demands for usage in challenging environmental conditions. The characteristics of being both aesthetically pleasing and durable are notable.
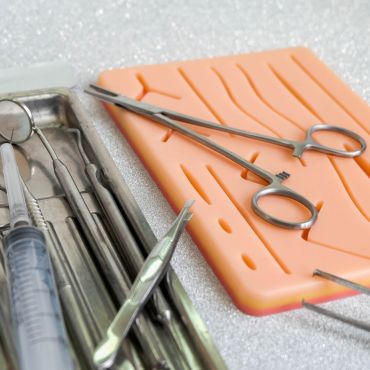
Zinc alloy die casting molds are widely utilized in the medical equipment industry, including:
- Housings for medical instruments.
- Components for medical devices.
- Parts for medical equipment.
Zinc alloy die-castings products produced using molds designed and manufactured by Yontone exhibit excellent biocompatibility, meeting the requirements for medical devices used within the human body. Simultaneously, they demonstrate good corrosion resistance, fulfilling the demands for medical equipment used in processes such as sterilization and disinfection.