Aluminum die-cast pans, wok pans, and BBQ pans are cookware that we use in our daily lives. They are in direct contact with the food, and need to treat the surface of the pot after the die casting. The usual surface treatment has a Teflon anti-stick treatment on the inner wall of the pan. Spray paint or plastic spray treatment of the appearance of the pot. And the bottom iron sheet processing for the use of the induction cooker.
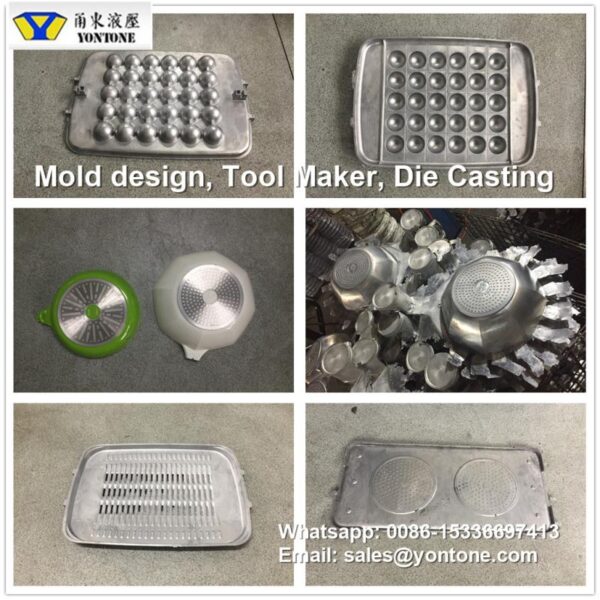
Die Casting Molds & Aluminum Die-cast Pot, please contact us!
sales@yontone.com;
Whatsapp:0086-15336697413
Frying pans, pots, flat-bottomed baking pans are mostly produced by aluminum alloy die-casting.
Our company has rich experience in producing moulds and products for all kinds of cookware.
Including all kinds of aluminium die-cast pots and aluminum die casting lids.
The aluminum die-casting parts produced by the mold we designed are well formed, easy to remove the runner & engate, easy to deburr, so customers purchase molds from us, produce die-casting in their factory is very efficient.
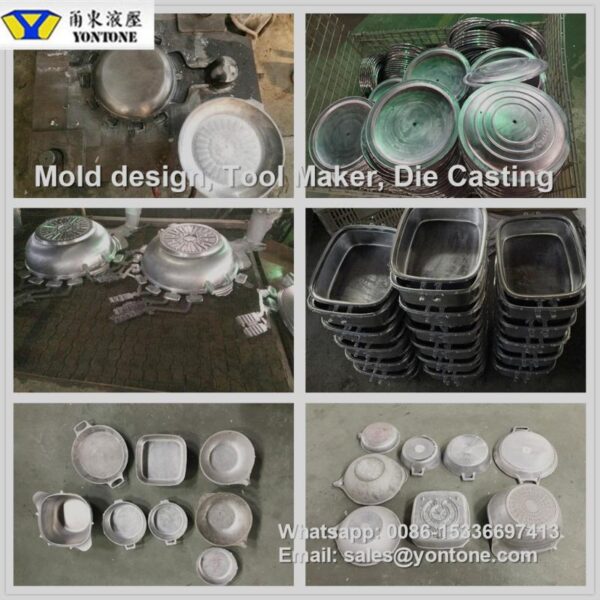
Aluminum alloy is the most widely used cookware material in the world because of its light weight, fast heat conduction and easy processing. The vast majority of all kinds of non-stick pans also use aluminum alloy as the base material. The processing and forming methods of aluminum alloy cookware are mainly divided into two categories: deformed aluminum alloy sheet pressing (deep drawing, spinning, etc.) forming, casting aluminum alloy casting (die casting, casting) forming. The most common aluminum alloys used for deep drawing are aluminum-manganese (3XXX) alloys, 3003 or 3103A are common types. Among casting alloys, ZL102 alloy with a silicon content of 10-13% is most commonly used for die casting; generally, there is no specific grade for casting, and the silicon element is generally less than 5%.
1. The difference between aluminum alloy die-casting pot and aluminum alloy stretching pot
a. shape.
The shape of the aluminum alloy die casting pot is more variable. The connection of the handle can be integrally formed with the pot body by die-cast.
The shape of aluminum alloy drawing pot is relatively regular. Required for connection to handle, welded fittings, welded to the body of the pot.
b. Heating uniformity, and deformation.
The heating effect of the aluminum alloy die-casting pot is better and more uniform than that of the aluminum alloy stretching pot. After the aluminum alloy stretching pot is heated, it is easier to deform than the aluminum alloy die-casting pot. The deformation is similar to the deformation of the pan raised bottom in the picture below.
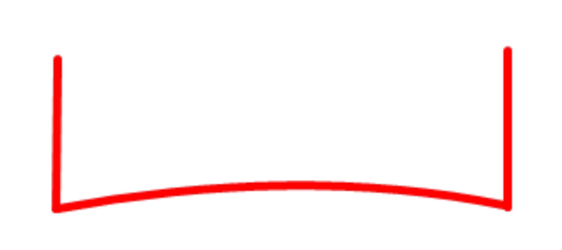
c. Cost
The mold of the aluminum die-casting pan, as well as the aluminum die-casting pan itself, will be more expensive than the aluminum stretching pan mold and drawing pan.
d. Lifetime
Aluminum die-cast pan’s thickness is relatively uniform. Aluminum stretch pan due to its craftsmanship, it will result in uneven thickness of the pot. Overall, aluminum die-cast pans last longer. More efficient use.
2. Other types of aluminum alloy pots
In addition to aluminum die-cast pans and drawing pans, there are several other aluminum pans that are made by different processes.
a. All aluminum alloy pot.
Generally, the surface treatment made of three-series aluminum alloy is generally polished and whitened. Another feature of the aluminum alloy pot is that it is easy to turn black if it comes into direct contact with the ingredients.
Pure aluminum is poor in strength, but light in weight, so it is no longer used.
b. Coated aluminum pan.
The largest amount of aluminum foil is various non-stick organic coatings, and the inner surface is non-stick coating, mainly polytetrafluoroethylene. There are also a few ceramic coatings that are polysiloxanes. The outer surface has enamel, high temperature paint, non-stick coating, hard oxidation, natural color aluminum, etc.
i) Choose a non-stick coating for the outer surface, which can increase the ease of cleaning of the outer surface. But the disadvantage is more obvious. The inner surface of PTFE is not easy to exceed the maximum temperature, and if the outer surface directly contacts the flame, the temperature will be very high, and it is easy to produce many harmful substances, such as perfluoroisobutylene polycyclic aromatic hydrocarbons.
ii)If high-temperature paint is used on the outer surface, the disadvantage is that the paint is easy to soften when heated by an open flame, and it is also easy to produce polycyclic aromatic hydrocarbons. In addition, many high temperature paint use epoxy resins, and there is a risk of releasing bisphenol a.
c. Anodized aluminum pot
Another major category of aluminum alloy pots is anodized aluminum alloy pots, the surface of which is anodized. A common anodizing treatment is oxalic acid oxidation( Natural color), sulfuric acid anodizing (Imitation porcelain), hard anodizing, etc.
The stability of the anodized aluminum alloy pot under neutral conditions is much higher than that of pure aluminum pot. Usually neutral salt spray test, test 192 hours are not easy to appear white rust( Alumina hydrate), usually untreated pure aluminum pans will show severe white rust within 8 hours.
However, under acidic conditions, especially organic acids such as citric acid, the corrosion rate of the oxide film is faster than that of pure aluminum pots. Take China’s 4%, acetic acid boil for 0.5 hours, and then soak for 24 hours in the test method. The US value is generally 8 to 10 ppm. Anodized films can exceed 50 ppm. So the anodized inner film aluminum alloy pot best not for cooking acidic foods. Such acidic foods generally have a PH value of less than 3, such as vinegar and pure lemon juice, but some weakly acidic ingredients are fine. Aluminum alloy anodizing pot, under the condition of PH value>4, the anodized film is still very stable.
Now anodized pots are rarely seen on the market, but common pressure cooker products still use anodized. The pressure cooker has strength requirements for the material of the pot body due to safety requirements. The production process of the usual non-stick coating needs to be sintered at a temperature of more than 400 degrees to reach the annealing temperature of the aluminum alloy, resulting in the failure pressure of the pressure cooker not meeting the standard. The pressure cookers we use in China generally carry out oxygen oxidation, and the pressure cookers in other countries generally use pure aluminum pots directly.
Conventional anodized films are soft in texture and are easily damaged by metal shovels or steel balls. Well, today we will focus on hard anodizing. According to GBT198822-2005, hard anodized oxide film of aluminum alloy, the specification stipulates that the anodized film is thick and hard, with a thickness of more than 25 microns and a microhardness of more than 400HV. Normal use will not be damaged by metal shovels and steel balls. It is not only suitable for pressure cookers, but also for aluminum alloy frying pans. In addition, the bottom layer used for non-stick coatings can greatly improve the service life of non-stick coatings.
d. Pressure casting aluminum pot/ pan
There are few cast aluminum pans on the market now. Among the common cast aluminum alloys that require fluidity in aluminum alloy casting, aluminum-silicon-based casting alloys have the best fluidity. Therefore, the cast aluminum alloys in the cookware industry are basically all aluminum-silicon-based silicon content, ranging from 3% to 13%.
Casting methods include die casting pot and casting pot.
The aluminum alloy die-casting pot can achieve a relatively thin pot body, and the production efficiency is high. Aluminum alloys need to use high-content silicon, and the silicon content is generally 10% to 13%. Aluminum die-casting pots will be made into coated pots in the future.
The cast aluminum pot is relatively heavy, and the production efficiency is low, and the output is relatively small. But low content silicon cast aluminum can be used. The silicon content is generally 3% to 5%. The benefit of compliance assistants is that they can use the technology of hard anodizing.
3. Summarize
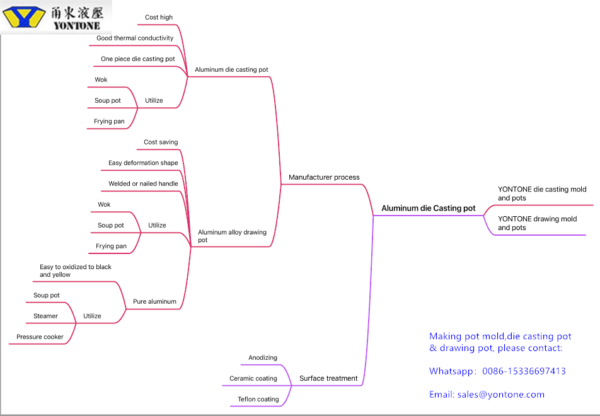