Based on the unique composition and physical properties of the materials, we carefully consider factors such as tensile strength, ductility, flowability, and chemical element content, to select the most appropriate materials for various applications. By choosing high-quality materials, our products exhibit superior mechanical properties, enhanced durability, increased strength, and exceptional oxidation resistance.
Product Material
The selection of materials plays a vital role in determining product properties, including strength, plasticity, hardness, and corrosion resistance. We carefully consider the customer’s specific product requirements and order quantity to provide recommendations on suitable mold and raw materials.
Our goal is to achieve optimal product outcomes while maximizing efficiency and cost-effectiveness.
We will provide corresponding material reports for each batch of products shipped. Below are material reports for some materials for your reference.
QT450 Ductile Cast Iron with Spheroidal Graphite is a high-performance material. It offers superior mechanical properties compared to gray iron and is similar to steel. It excels in casting, cutting, and wear resistance, while also providing excellent elasticity.
A357 is a cast aluminum alloy consisting of 6.5 to 7.5% silicon, 0.04 to 0.07% beryllium, 0.2% iron, 0.2% copper, 0.4 to 0.7% magnesium, 0.04 to 0.2% titanium, 0.1% zinc and 0.1% manganese. It has excellent strength and performance, and can be further enhanced through heat treatment.
ADC12, or A383, is a widely used aluminum alloy for cost-effective die-casting components, popular in China and internationally.
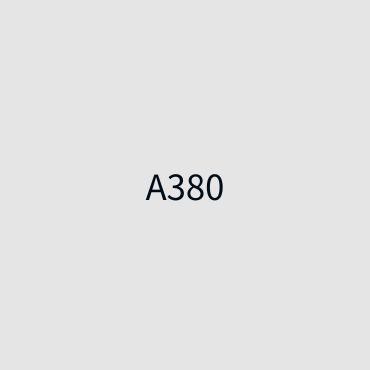
A380 Composition: Aluminum: 90%; Copper: 6%; Magnesium: 3%; Others: 1%. It possesses high strength, excellent corrosion resistance, and good weldability. A380 is primarily utilized in aerospace, automotive manufacturing, and construction industries.
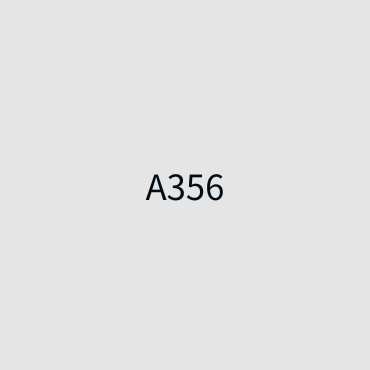
A356 Composition: Aluminum: 97%; Silicon: 2.5%; Magnesium: 0.5%. It exhibits high strength, excellent heat resistance, and good machinability. A356 is primarily used in aerospace, automotive manufacturing, and mold manufacturing industries.
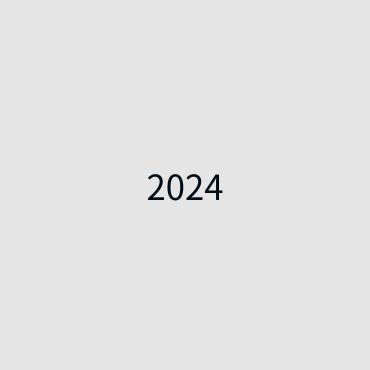
2024 Composition: Aluminum: 94.7%; Copper: 4.0%; Magnesium: 1.3%. It exhibits excellent machinability, high strength, corrosion resistance, and good weldability. 2024 is primarily used in the aerospace, automotive industry manufacturing, and construction industries. It can achieve T4 temper through heat treatment.
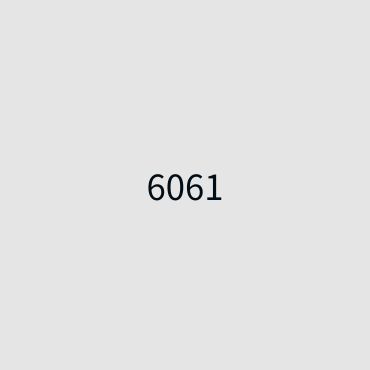
6061 Composition: Aluminum: 96.1%; Magnesium: 0.6%; Silicon: 0.3%. It possesses high strength, corrosion resistance, and good machinability. 6061 is primarily used in aerospace, automotive manufacturing, and construction industries. It can achieve T6 temper through heat treatment.
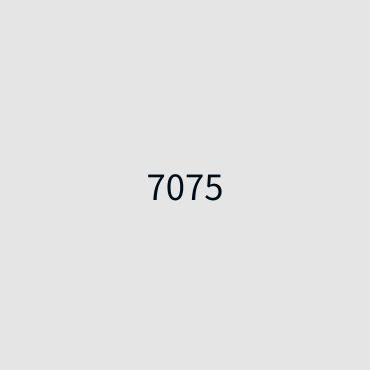
7075 Composition: Aluminum: 91.5%; Zinc: 5.2%; Copper: 2.5%; Magnesium: 0.8%. It boasts the highest strength and corrosion resistance but comes with lower machinability. 7075 is primarily used in the aerospace, automotive manufacturing, and construction industries. It can achieve T6 temper through heat treatment.
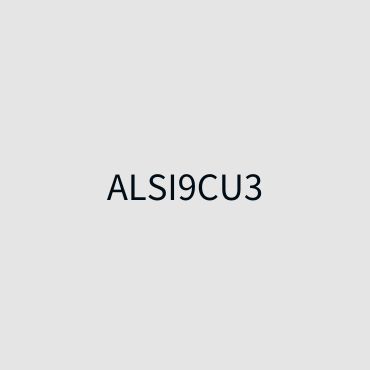
AlSi9Cu3 Composition: Aluminum (Al) Balance, Copper (Cu) 2.0-3.5, Silicon 8.0-11.0. This alloy, as a typical representative of aluminum-silicon alloys, is known for its high strength, excellent corrosion resistance, and fatigue performance. It is commonly used in automotive structural components and electronic appliances.
Mould Material
We employ a variety of materials for mold components, including the cavity, frame, ejection pin, and slider block. The selection of mold materials is a critical factor influencing both product molding and mold lifespan.
Commonly used materials for mold cavities include H13, Dievar, C45 steel, and others.
Heat Treatment Report
Heat treatment is a crucial process for enhancing the properties of both products and molds.
Below are samples of our heat treatment reports, click on the image to access the corresponding heat treatment report.: