What are Brass Casting Molds?
Brass casting molds are designed based on the shape, dimensions, and performance requirements of the product. They are utilized in the process of low-pressure casting, gravity casting, sand casting, or high-pressure die casting, where the molten brass alloy is injected into the mold and, upon cooling, produces the cast component. This tool can be categorized into brass sand casting molds, brass investment casting (lost wax casting) molds, brass gravity casting molds, and brass die casting molds, depending on the casting process.
Mold Different Brass Casting Process
Yontone provides mold design and manufacturing services for various brass casting processes.
Among them, sand casting and investment casting (lost wax casting) do not utilize metal molds. Gravity casting and die casting, on the other hand, employ permanent molds.
Brass gravity casting and brass die casting utilize permanent molds made of metal. For brass die casting molds, due to the higher casting pressures and brass melting point being high up to 900degree centigrade even over 1000, Yontone uses heat-resistant die steels to enhance the mold’s durability against the increased impact and stresses, thereby extending the mold’s lifespan.
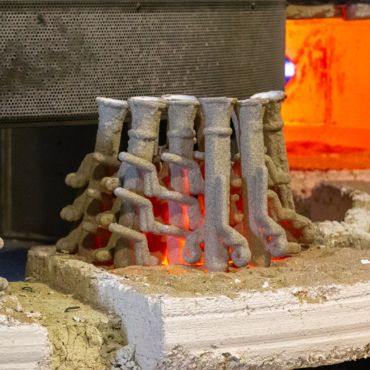
Using wax to replicate the product model, immersing it in coating material to form a refractory coating, and melting the wax mold in an oven to create a cavity. This cavity can be utilized for brass investment casting. So-called investment casting molds.
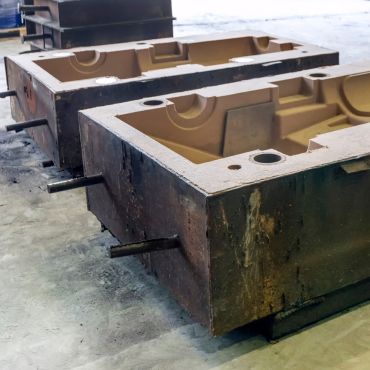
Creating a model based on the shape of the product, placing it into casting sand, compacting and sintering to form a sand mold. Removing the model, pouring molten brass into the sand mold to fill its cavity, resulting in the final brass sand cast part. This sand mold is what we refer to as a brass sand casting mold.
Brass Casting Ways to be Choosen
The manufacturing and post-production costs vary for different types of brass molds.
When providing custom brass casting molds, Yontone takes a customer-centric approach. We consider factors such as part size, order batch quantity, precision, appearance requirements, airtightness requirements, complexity of structure, and the ultimate purpose of the customer’s product.
Based on these considerations, we recommend the most cost-effective and reasonable brass casting process for our customers.
Below are some custom brass casting parts for your reference.
Advantages of Brass Casting Molds
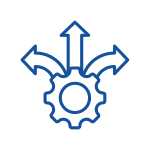
Brass sand casting molds are cost-effective and capable of producing extremely large-sized brass products.
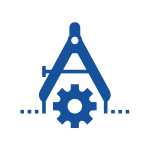
Brass gravity die casting molds can produce highly precise brass products.
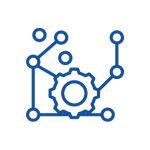
Brass investment casting mold (lost wax casting) can produce the most complex brass castings.
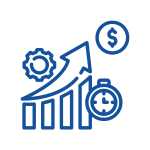
Brass pressure die casting molds can efficiently and rapidly produce brass products.
Experienced Brass Casting Mold Designer
Yontone’s team of mold designers, drawing upon years of design experience and incorporating mold flow analysis, creates well-designed molds for brass sand casting, gravity die casting, and pressure die casting.
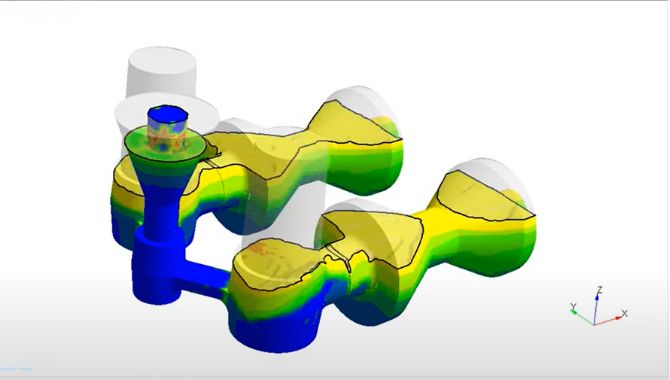
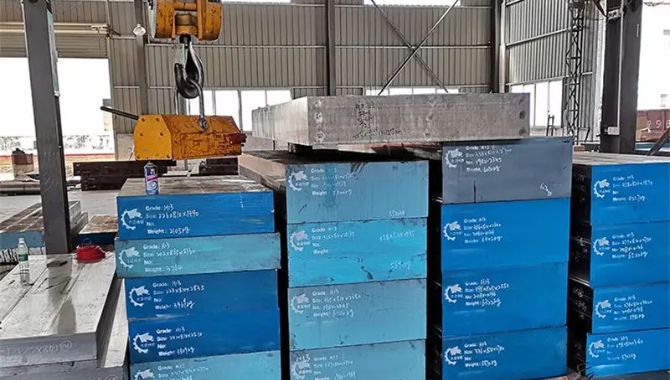
Brass Casting Mold Materials
Based on the order quantity, complexity of the product, and surface finish requirements, Yontone uses different mold materials for various casting processes. The mold material selection varies:
- For brass pressure die casting molds, Yontone typically uses hot work tool steels, with H13 being a common choice, while higher specifications may involve the use of imported tool steels.
- For brass gravity die casting, mold materials such as aluminum alloys like 7075 or cast iron HT200 can be employed.
- Other brass casting processes, such as sand casting and lost wax casting, may involve the use of mold materials like beryllium copper (C17200), graphite, and casting sands.
This diverse selection of mold materials allows Yontone to tailor the choice to specific casting requirements, ensuring optimal performance and quality based on the characteristics of each casting process.
Quality Control
All products produced through Yontone brass casting molds undergo rigorous inspection. We provide material and dimensional reports along with each order for brass castings.
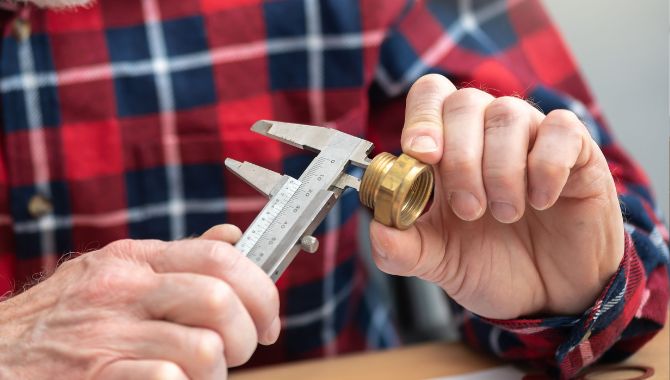
Why Choose Yontone to Be Your Brass Casting Supplier?
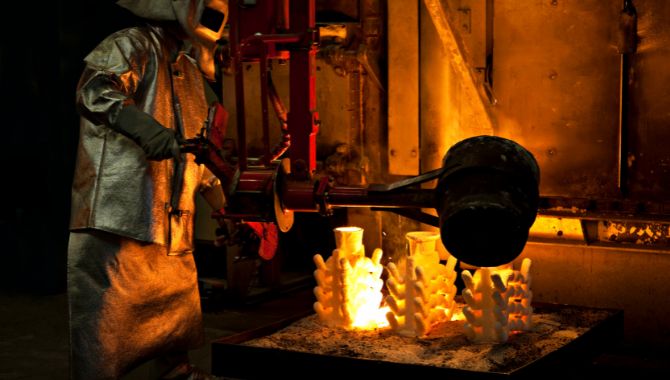
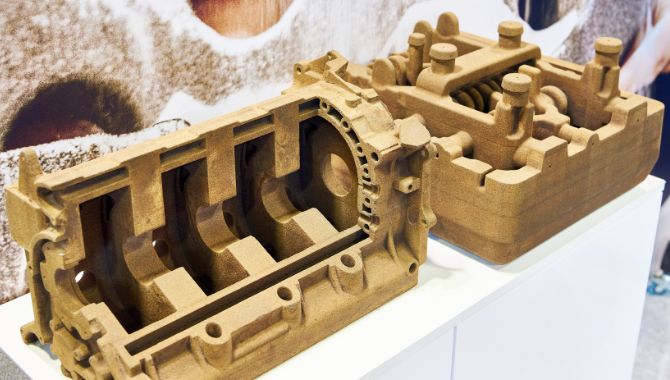
- Yontone has a complete brass casting production line, from manufacture brass casting molds to brass casting to brass machining and surface treatment.
- Yontone provides various brass casting methods to meet your order requirements, offering very low MOQ (minimum order quantity).
- All products cast by us undergo a stringent inspection process, ensuring that customers receive qualified products.
- Yontone ensures timely delivery, and if you are unfamiliar with the import process, we can handle it for you, allowing you to simply receive the goods.
- Trustworthy company: Yontone has been thriving in the mold and brass casting industry for several decades. We are committed to contributing our expertise and capabilities to assist customers in designing and producing molds that are efficient, high-quality, and precise.
Wild Application Fields of Brass Casting Molds
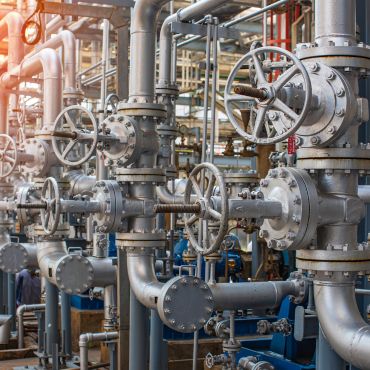
In the application of industrial valves and pipeline components, brass lost wax casting is a common and effective manufacturing process. Here is a detailed explanation of the specific application of brass lost wax casting in these applications:
Valve Component Manufacturing: Brass lost wax casting is used to produce various components of industrial valves, including valve bodies, valve covers, valve seats, valve stems, etc. The high precision and good surface quality of lost wax casting ensure the sealing and operational performance of the valves.
Production of Pipeline Connectors: Industrial pipeline systems require various connectors such as elbows, flanges, and pipe fittings. Brass lost wax casting is used to manufacture these connectors, ensuring their accuracy and strength to meet engineering requirements.
Manufacturing Precision Components: Industrial valves and pipeline components often require some complex and precise components, such as control valves and check valves. Brass lost wax casting can produce complex-shaped and dimensionally accurate components to meet the high requirements of industrial applications.
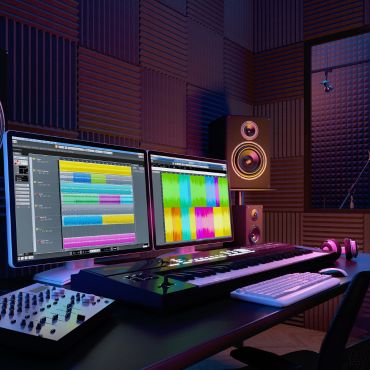
- Brass, known for its excellent thermal conductivity, is utilized in brass casting molds for manufacturing heat-dissipating components such as heat sinks and radiators.
- Brass, with its inherent corrosion resistance, allows casting molds to deliver high-precision surface quality, meeting the aesthetic design requirements of electronic products.
- Brass casting molds are also capable of producing precision-turned and shaped casing components for electronic devices, providing an elegant appearance.
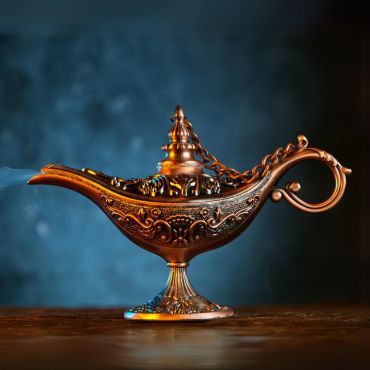
The brass investment casting mold technology is widely used in the field of art and sculpture due to its high precision and ability to preserve details. This method allows artists to create more intricate and delicate works while maintaining the strength and texture of the material. Brass castings are often crafted into items such as door handles, decorations, and more.
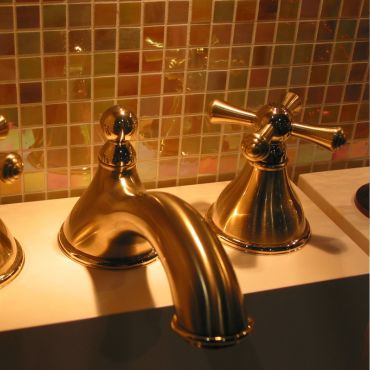
Brass gravity die casting molds are commonly utilized in the production of key components for bathroom brass fixtures and brass faucet parts. This casting method plays a crucial role in providing high precision and complexity for bathroom products. Through gravity die casting, precise control over the shape and structure of bathroom brass fixtures is achieved, ensuring they meet design specifications and possess a desirable texture. This process efficiently produces brass bathroom products with excellent performance and visual appeal, meeting the high standards of the market and consumers for quality and design.