What is brass die casting?
Brass die casting is a process where molten brass alloy is injected into a metal mold using a cold chamber die casting machine. The alloy then cools and solidifies under high pressure, resulting in the formation of the brass castings.
It’s quite important during the die casting process to maintain the mould also.
Brass die casting has the following main characteristics:
- The mechanical and wear resistance properties of brass alloy die-cast products surpass those of aluminum alloy die casting and zinc alloy die casting.
- It exhibits strong corrosion resistance in both atmospheric and seawater environments.
- Excellent electrical and fluid conductivity.
- Possesses anti-magnetic properties, making it suitable for manufacturing instruments and components that cannot tolerate magnetic field interference.
Brass alloy’s higher melting point compared to aluminum alloy allows for metal liquid temperatures of up to 800-1000°C during copper die casting, posing a greater impact on the distortion of mold materials. It’s quite important to maintain the mould during the die casting process.
Brass alloy die casting molds have a short lifespan, and incur high costs. Therefore, for complex brass products with less stringent density requirements, casting, sand casting, forging, and other methods may also be employed.
Brass die casting parts offers higher production efficiency compared to copper alloy casting and sand casting. It provides good surface finish, high dimensional accuracy, and supports automated production.
Yontone offers brass die casting service and brass die casting mold making service as a pack solution.
Brass Die Casting Parts
The following brass die-cast products are provided solely for customer reference.
Yontone offers custom brass die casting services based on your drawings or by sending samples to us. We will measure the samples, create drawings, manufacture molds, and proceed with die-casting production.
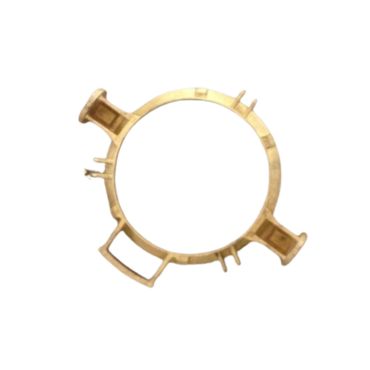
In the image, copper die-cast products resembling portholes are produced using cold chamber die-casting machines.
For brass die-cast products, we typically employ simple polishing or sandblasting, along with transparent paint spray on the surface, to retain the naturally appealing brass color. This provides a protective layer for the brass products, preventing oxidation and corrosion.
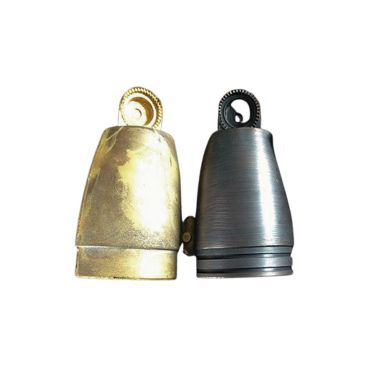
Antique-style Surface Treatment for Brass Die Casting. In the picture, left side is the brass die casting lamp cover without surface treatment, right one is brass die casting light housing with antique-style surface treatment.
Such antique-style surface treatments give brass products a more historical and unique appearance.
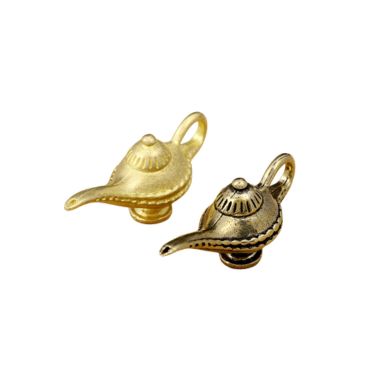
Brass die-casting is often used for crafting artistic pieces, including figurines and other decorative items.
In the image, the left part retains the natural color of brass through die-casting, while the right one undergoes a different antique bronze treatment, distinct from the one shown in Figure 2.
Brass Die Casting Process Step By Step Guide
The brass die-casting process is relatively simple:
Melting Brass Material: Brass material is melted.
Injecting Molten Brass: The molten brass solution is introduced into the feed tube of the die-casting machine.
Die-Casting Process: During the die-casting process, a piston pushes the molten brass solution into the brass die-casting mold, filling the entire cavity.
Cooling and Solidification: After the brass solution cools and solidifies, a plunger ejects the brass casting from the mold.
Removing Gates, Runners, and Flash: Gates and runners are removed, and any excess material (flash) is trimmed.
Polishing or Surface Treatment: The finished brass casting may undergo polishing or other surface treatments.
This process results in the creation of brass die-cast components, and the final steps may include additional finishing processes to achieve the desired appearance and quality.
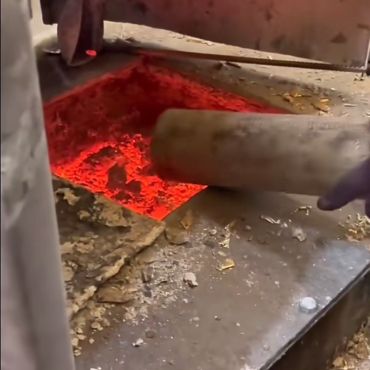
The temperature for brass die-casting typically ranges between 900-1000°C, necessitating a crucible with enhanced heating and insulation capabilities.
In China, HP59-2 is the common material used for brass die casting, although other materials such as copper or bronze can also undergo die-casting processes.
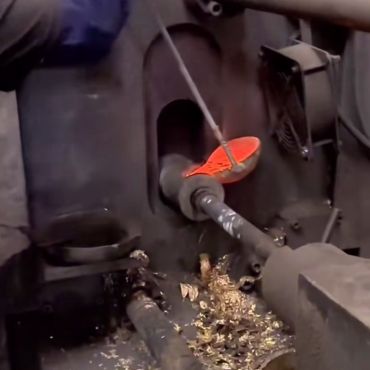
After the die-casting worker pours molten brass into the feeding tube of the die-casting machine, the piston rapidly and forcefully pushes the brass liquid into the mold cavity.
The mold remains closed for a specified duration, allowing the brass castings to cool and solidify.
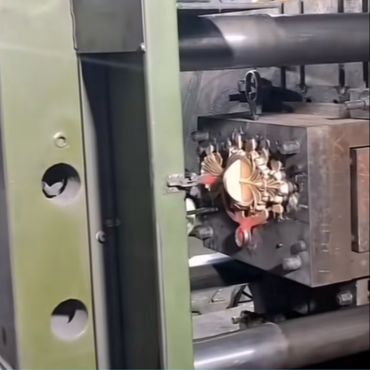
After the mold opens, the brass die-casting part is ejected using an ejection pin, and a worker then retrieves the brass castings from the mold.
Operators need to inspect the appearance of each product, separating those that meet the quality standards from those that do not.
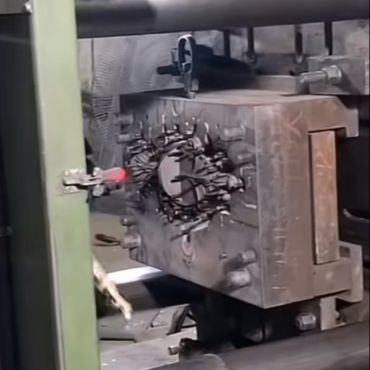
After removing the brass die castings from the mold, the worker sprays the mold and checks for any stickers. If stickers are present, they clean the affected area and prepare for the next round of brass die casting.
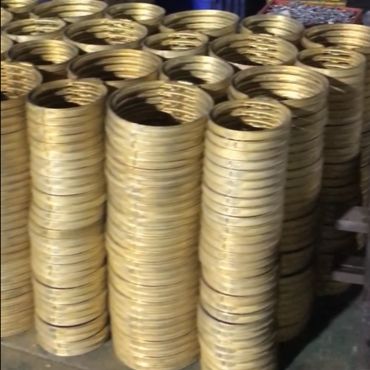
Specialized workers will trim or deburr brass die castings, removing the gate, runner, and flash before setting the castings aside.
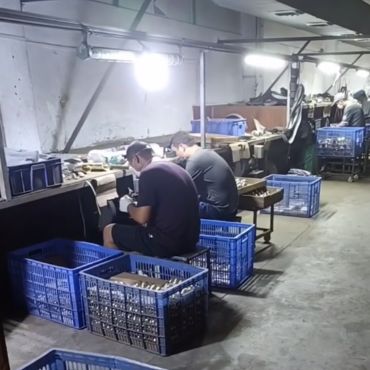
Brass die-cast components used for aesthetic purposes undergo surface treatment, whether it be sandblasting, polishing, or painting, to ultimately achieve an attractive appearance.
Advantages of Brass Die Casting Parts
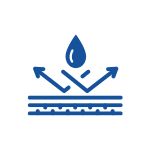
Brass die-cast components exhibit outstanding corrosion resistance than aluminum die casting and zinc die casting parts.

Brass die casting parts exhibit efficient electrical conductivity. Copper, the primary component of brass, is a superior conductor of electricity, second only to silver.
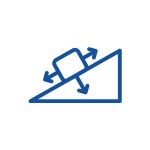
Brass is a metal alloy composed of copper and zinc, exhibiting a relatively low coefficient of sliding friction, this performance characteristic extends the service life of brass die casting parts.
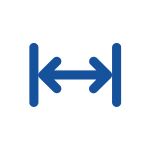
Brass die casting parts have excellent elongation and tensile strength, enabling these components to withstand certain forces and strains in various applications while maintaining their shape and structural integrity.
Brass Die Casting Mold
Due to the high molten temperatures in brass die casting, it is a significant challenge to the longevity of the molds.
- Yontone places higher quality standards and design requirements on the material and structure of brass die casting molds compared to those for aluminum and zinc alloy die casting. The objective is to provide customers with relatively long-lasting brass (copper alloy) die casting molds.
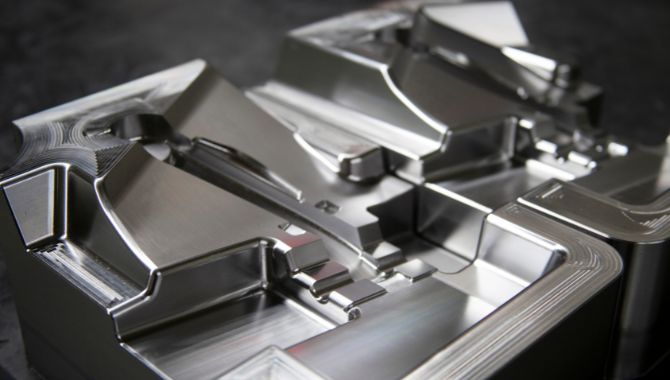
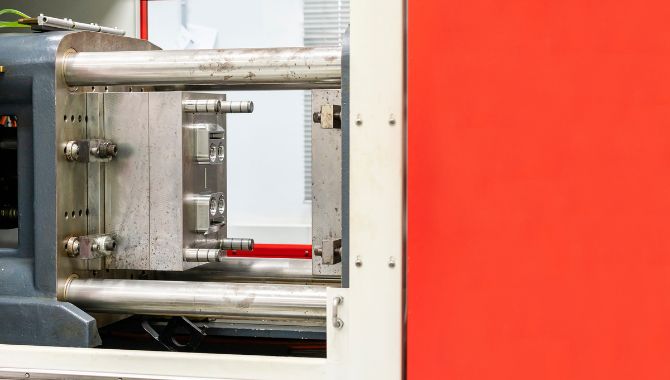
Brass Pressure Die Casting Machine
Same as aluminum alloy die casting, brass (copper alloy) die-cast products also utilize cold chamber die-casting machines, and the crucible temperature for copper alloy die casting can reach over 1000°C.
- Yontone company offers copper alloy die casting services ranging from 280 tons to 800 tons.
Machining and Surface Treatment
In addition to brass die casting services, Yontone factory also provides CNC machining based on customer drawings.
Also Yontone provides surface treatment services like sand blasting, polishing, chrome coating, powder coating, paint, etc.
This allows customers to receive products that are ready for assembly and immediate use.

Why Choose Yontone to Be Your Brass Die Casting Supplier
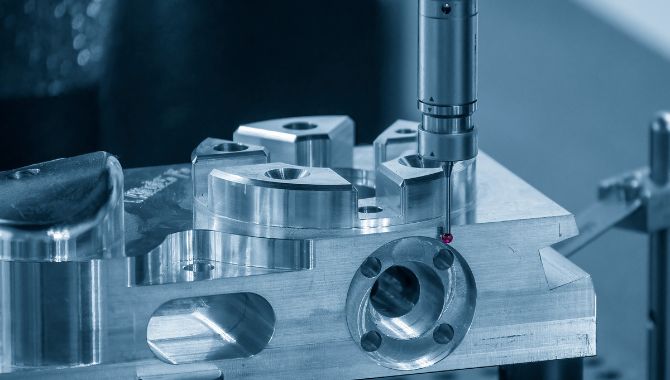
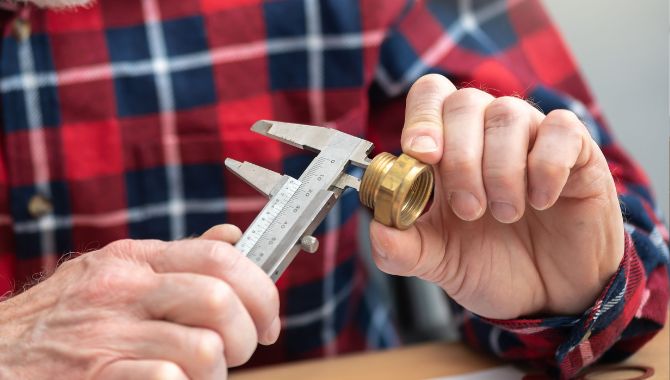
With decades of experience in mold production and die casting, Yontone boasts a professional team of designers and die-casting operators. Tailoring our expertise to the specific characteristics of (copper alloy) brass die casting, Yontone has dedicated mold designers and die-casting parameter engineers. Considering brass’s flowability and shrinkage, well-designed molds and die-casting processes are implemented to minimize the risk of internal porosity in brass die-cast products.
- Reasonable mold structure ensures high production efficiency in brass die casting, with easy demolding and prolonged mold lifespan.
- Low minimum order quantity: Yontone accepts orders for copper alloy die-cast products ranging from hundreds to several hundred thousand pieces, with pricing based on quantity, offering quotes with different quantity ranges.
- Stable lead times: Lead times are communicated before placing an order, and Yontone consistently delivers orders on time.
- Real-time reporting: Weekly progress reports with photos and videos allow customers to monitor the production status of their orders in real-time.
- Competitive pricing: Yontone delivers five-star quality at three-star prices, offering high-quality products at competitive rates.
- Quality control: Yontone maintains strict quality control, incorporating self-inspection during die-casting, regular inspections, and pre-delivery random sampling. Inspection reports are provided according to customer requirements.
Reliability and trustworthiness: Yontone aspires to be a company that lasts for decades, prioritizing integrity as the lifeblood of the business. Our commitment is to deliver high-quality products to customers on time.
Wild Application Fields of Brass Die Casting Parts
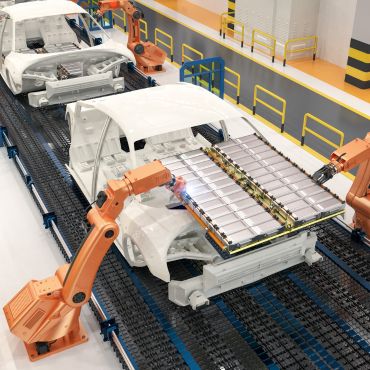
The low-friction properties of brass die casting components reduce energy consumption and minimize wear at friction points, thereby extending the lifespan of components. This characteristic makes brass die casting components widely applicable in scenarios where reducing friction and enhancing wear resistance are crucial, such as in mechanical equipment, automotive components, and various engineering fields.
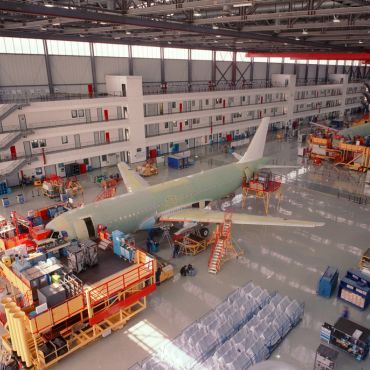
The excellent elongation and tensile strength characteristics of brass die casting components make them an ideal choice for manufacturing parts that demand high strength and toughness. This is particularly true in applications within the aerospace industry and other areas requiring high-performance materials.
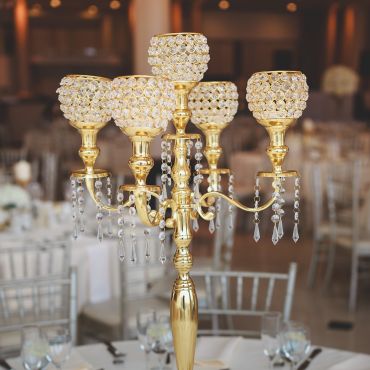
Brass die casting parts have extensive applications in the field of decorative items, Art and Sculptures, Home Decor, Jewelry and Accessories, Furniture Decoration, Lamp Accessories, Antiques, and Antique Decorative Items.
The application of brass die casting parts in the field of decorative items provides designers and manufacturers with a rich array of options, ensuring that decorative pieces not only possess artistic and aesthetic qualities but also exhibit the unique texture and durability of brass.
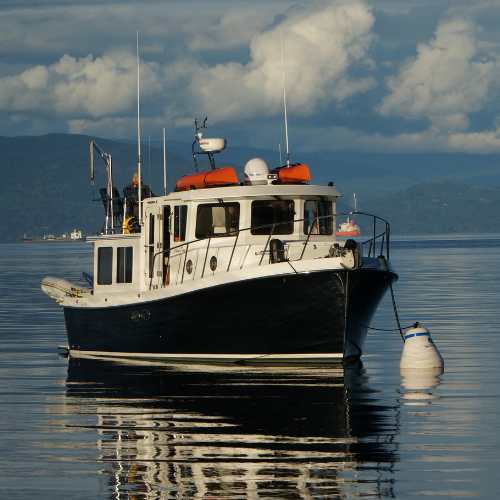
Brass die casting parts possess high corrosion resistance, contributing to their extensive utilization in diverse fields like marine engineering and chemical equipment. Their ability to withstand the impacts of humidity, salt, and other corrosive elements makes them exceptionally well-suited for applications where corrosion resistance is crucial.
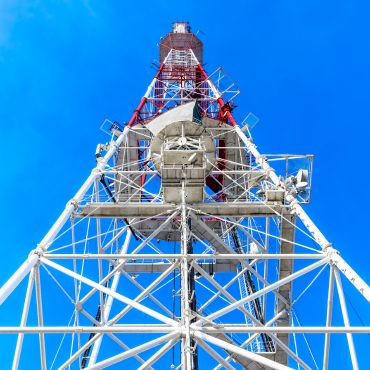
Brass die casting parts are also utilized in:
Communication Equipment: Including the manufacturing of outer casings and internal components for communication devices.
Medical Equipment: Used for producing components for medical devices and instruments.