What is Gravity Casting?
Gravity casting (also called “gravity die casting) is a metal casting process that uses the gravity of the earth. Molten metal is poured into the mold sprue without applying any pressure, the liquid flows slowly into every corner of the mold, filling the cavity, allowing for venting, and cooling, and then the mold is opened to obtain the gravity casting products. This process is particularly suitable for manufacturing products with thicker wall sections.
In a broad sense, gravity casting includes a variety of methods, such as sand casting, metal mold casting, investment casting, lost foam casting, and clay mold casting.
However, in a narrow sense, gravity casting usually refers to the two main methods of sand casting and metal mold casting. These methods rely on the Earth’s gravity to achieve high-quality casting product manufacturing.
On this page, we are talking about gravity casting using a metal mould, the mould was made of heat-resisting steel alloy.
Gravity Casting Parts
Gravity casting products are more suitable for those whose thickness of the casting products are bigger than 8mm, there might be porosity if the parts are made by the die casting process, but gravity casting can handle such kind of products.
As gravity casting manufacturer, Yontone company supplies mainly: Aluminum Gravity Casting Parts and Zinc Gravity Die Casting Products
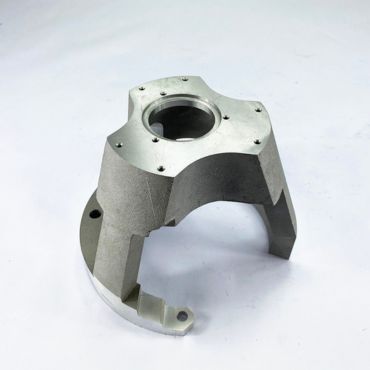
Different Applications of Gravity Casting Parts
Gravity Casting Process is used for the manufacturing of beams, steam turbine blades, pump housings, brackets, hubs, intake lips, and engine casings, among other components. It is also used in the production of automobile cylinder heads, transmissions, and pistons, as well as parts such as instrument enclosures and supercharger pump housings.
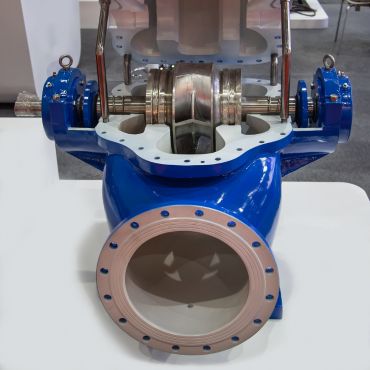
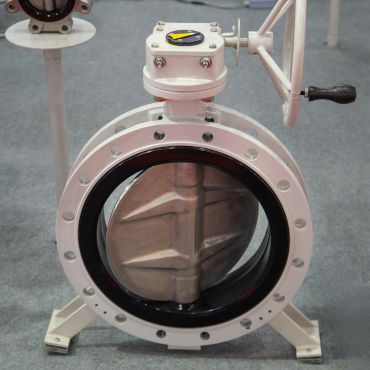
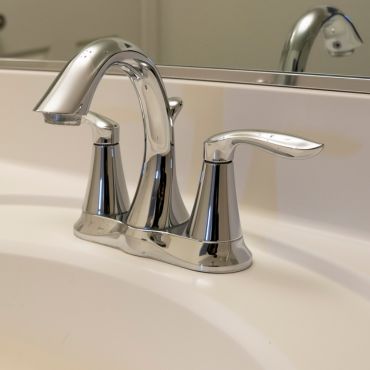
Gravity Casting Processes Step by Step
- Put sand core into the mold
- Pour molten aluminum alloy or zinc alloy liquid into a casting mold.
- Rotate the mould 90 degrees, from horizontal to vertical state, so the liquid goes inside the mold quickly and smoothly under the influence of gravity
- Wait for some time (a few seconds to a few minutes), waiting for the parts to cool down.
- After the parts are cured, reverse rotate the mould 90 degree, to make the mould back to the original position.
- Take out the finished gravity casting parts.
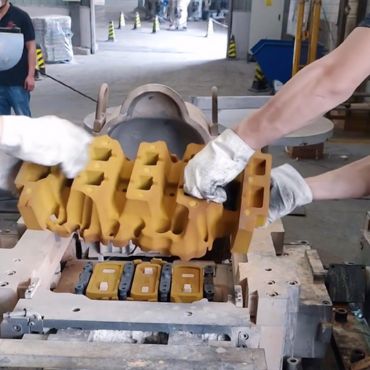
Put the sand core into the gravity casting mold, sand core will form the inside construction of the gravity casting parts. (gravity casting machine 180degree, lie down)
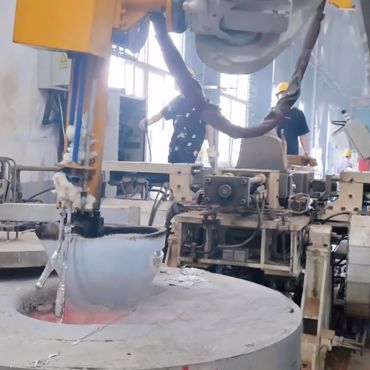
Using ladle to take melt metal liquid
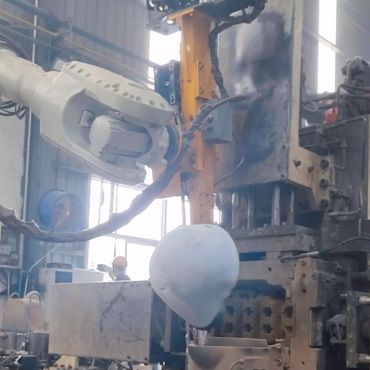
Pour the metal liquid into the gravity casting mold, and in the meantime, the gravity casting machine turn 90degree (stand up)
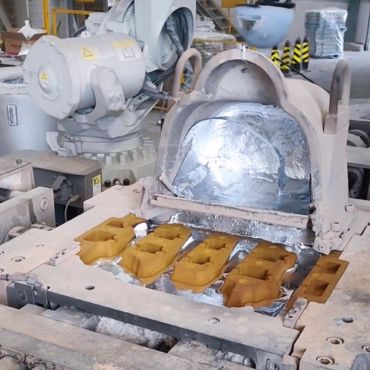
Metal liquid flows into the gravity casting mold, fills the whole mold. (Gravity casting machine lies down again.)

Wait until the metal liquid cure to solid. And take the gravity casting part out.
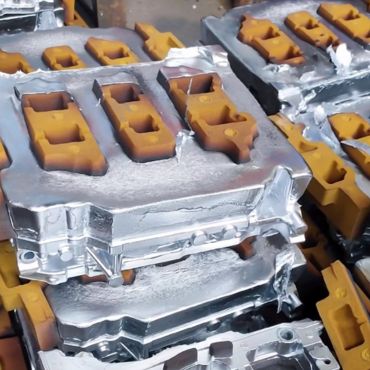
Finished gravity castings.
Advantages of Gravity Casting Process
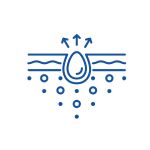
Compared with die-casting parts, gravity gravity-casting process can produce products with few internal pores, which have better air tightness. Suitable for thick wall parts.
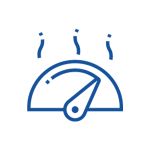
Gravity casting parts can be heat treated, after that, the product exhibits increased material hardness, strength, wear resistance, and corrosion resistance, thus enhancing product performance and longevity.

Low mold costs, and long mold lifespan. Particularly suitable for the production of large or extremely large castings in the shipbuilding and aerospace industries.
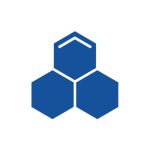
For products that require replicating intricate internal structures and cannot be achieved through a single die-casting process, gravity casting with sand core design offers a perfect solution.
Sand Core Function
In the gravity casting process, the sand core is mainly used to form the inner cavity and cavity of the casting. The sand core is made of casting sand, molding sand binder auxiliary additives, and other modeling materials mixed in a certain proportion. The main uses of the sand core are as follows:
- Form the inner cavity and cavity of the casting. The inner cavity and cavity of castings usually cannot be directly formed with metal, so sand cores are needed to form them. The sand core can be designed and manufactured according to the shape and size of the casting, has good strength and heat resistance, and can withstand the pressure and temperature of liquid metal.
- Improve casting quality. Sand core can effectively prevent defects such as pores, shrinkage cavities, and cracks in castings. The sand core has a certain degree of concession and can absorb the thermal stress generated by the liquid metal during the cooling process, thereby reducing the possibility of defects in the casting.
- Reduce casting costs. The cost of sand cores is relatively low, thus reducing casting costs.
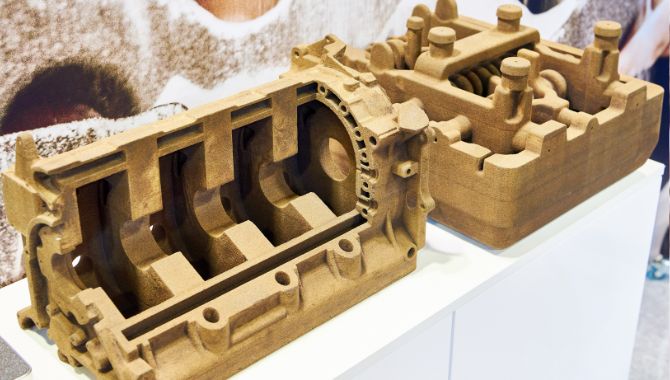
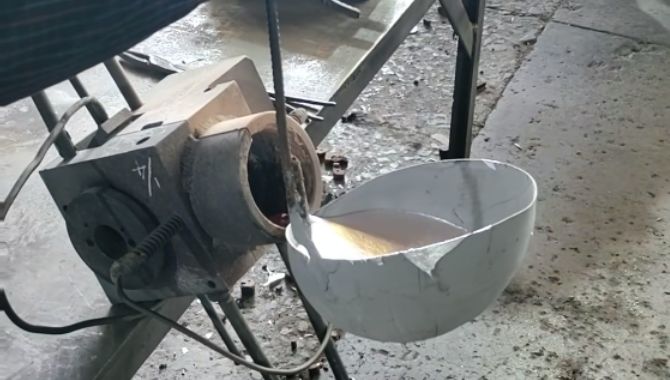
Hand Made Gravity Castings
For small, simple parts or small quantity orders, Yontone skilled casting workers use hand-made gravity castings.
This will save costs and shorten the setup time.
For gravity casting manufacturing methods, Yontone is quite flexible to meet all the client’s requests.
Quality Control
Yontone has a strict quality control system.
- We use CMM to check product dimensions, and 2D profile projector to measure product curves, surface profiles, and roughness.
- We have a strict incoming inspection process to ensure that the raw materials are good, so that the products are good.
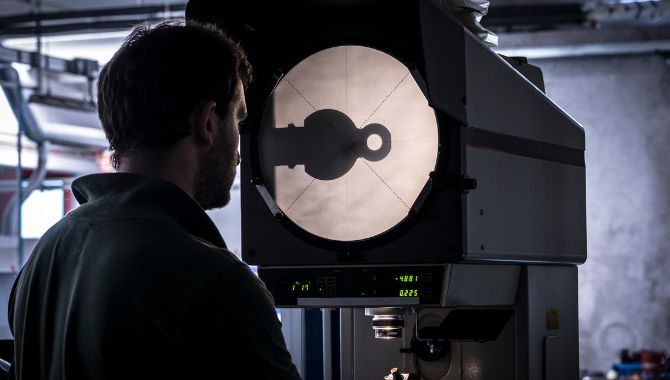
Why Choose Yontone as Your Gravity Casting Supplier

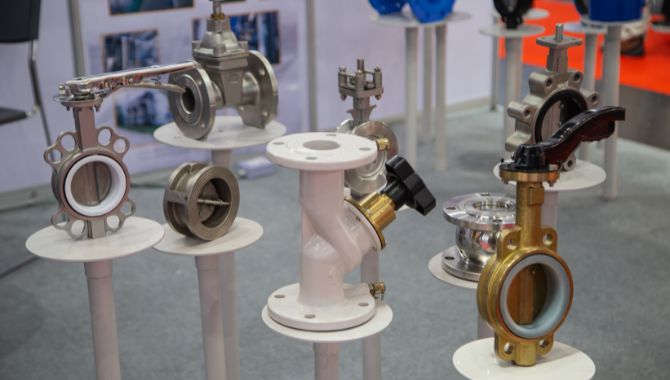
Our duty is to serve customers, so no matter the size of the product or the quantity of the order, we can perfectly meet customer needs.
- Experience: Yontone has been specializing in gravity casting parts for 20 years, offering a complete solution of gravity casting and machining services. Our experienced designers have over 8 years of gravity casting design experience.
- Delivery: Always on time. And update the production process weekly by email, video and pictures.
- Quality: High-quality gravity castings, high strength, high precision, less porosity, and we provide material certification, also offer a full-size report along with each shipment.
- Flexibility: With low minimum order quantities and reasonable pricing, we provide different quantity prices in our quotations.
Wild Application Fields of Gravity Casting
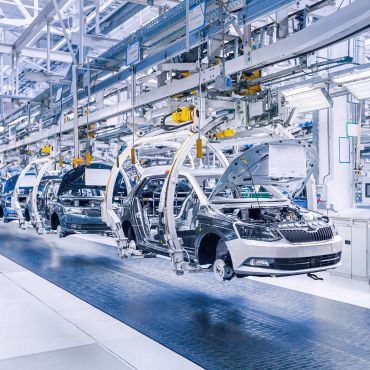
Yontone produces gravity castings with high strength, corrosion resistance, and wear resistance, meeting the high-performance requirements of automotive components. They are widely used in the automotive industry, including the manufacture of engines, transmissions, chassis, and body components.
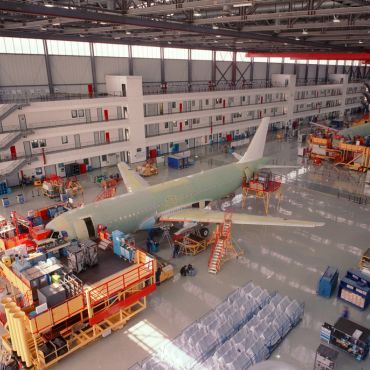
Yontone’s gravity casting products are widely used in the aerospace industry, for example, in the manufacture of engine, fuselage, and landing gear components.

Yontone’s gravity castings have high precision, high surface finish, and good mechanical properties, meeting the high-performance requirements of precision instruments. They are widely used in the precision instrument industry, including the manufacture of instruments, meters, and medical devices.

Yontone produces gravity castings with high conductivity, high insulation, and good mechanical properties, meeting the high-performance requirements of the electronic industry. They are widely used in the electronic industry, including the manufacture of motors, transformers, and capacitors.

Yontone’s gravity casting components are widely used in the mechanical manufacturing industry, including various mechanical parts, such as gears, shafts, housings, brackets, and connectors. And also various mechanical equipment parts, such as pumps, valves, pressure vessels, and machine tool parts.
These castings have high strength, corrosion resistance, wear resistance, and good mechanical properties, meeting the requirements of mechanical equipment in various working conditions.