What is Low Pressure Die Casting Process?
Low Pressure Die Casting (LPDC) is a process in which compressed air presses the metal liquid(in a crucible) to rise into the mold cavity, and then cools it down, to get the final casting products. It’s also known as low-pressure casting (LPC), the casting pressure falls between high-pressure die casting and gravity casting.
Low-pressure die Casting is commonly used for the production of high-quality, complex aluminum and magnesium alloy castings.
Its fundamental principle:
- introducing dry compressed air (or inert gas) into a crucible containing molten metal at a certain temperature, causing the molten metal to rise through a riser and enter the mold cavity through a sprue.
- Once the mold cavity is filled with molten metal, the air pressure is increased and maintained until the casting has completely solidified.
- Afterward, the pressure is released, allowing any remaining liquid metal in the riser and sprue to return to the crucible, completing the low-pressure casting process.
- The desired castings are obtained once the mold is opened.
Several factors influence low-pressure casting, including pressure, pouring temperature, pressure holding time, and mold temperature.
The technical characteristics of low-pressure casting, based on the principle of pressure casting, rely on creating a pressure differential between the metal’s surface and the mold cavity using equipment, allowing the metal to fill the mold from the bottom up. Low-pressure casting typically involves establishing a positive pressure within a holding furnace while the mold remains open to atmospheric pressure. The pressure differential in low-pressure casting is defined as the pressure inside the holding furnace minus atmospheric pressure.
- Adjustable Pressure and Speed during Pouring: Low-pressure casting allows for the adjustment of pressure and pouring speed, making it suitable for various casting types, such as metal molds, sand molds, and for casting various alloys and sizes of castings.
- Adjustable Pressure Curve: By configuring the pressure curve appropriately, the metal filling process becomes smooth, reducing or preventing turbulence and splashing of the metal, consequently reducing the formation of oxide slag.
- Bottom Pouring: Low-pressure casting utilizes a bottom pouring method, ensuring a slow and controlled filling of the metal without splashing. This approach minimizes the entrainment of gases and the scouring of mold walls and cores, ultimately improving the casting’s yield rate.
- Applications: The primary applications for low-pressure casting are traditional products, including cylinder heads, wheel hubs, cylinder blocks, and similar components.
Application of Low Pressure Die Casting Parts
Low-pressure die casting process excels in creating complex-shaped castings with stringent quality requirements.
- It is primarily used to manufacture a wide range of high-quality components for vehicles, including automobile, motorcycle, and aircraft wheel hubs, internal combustion engine cylinder blocks, cylinder heads, pistons, and more. It also serves in the production of automotive transmission housings, crankcase oil pans, turbocharger housings, and various suspension and chassis components, such as steering knuckles, control arms, calipers, subframes, and beams.
- This versatile process is also employed in crafting intricate castings, such as impellers, guide wheels, propeller blades, and unique components like fan blades. In the electrical power transmission sector, it’s used to create equipment and components, such as high-pressure switch housings, tanks, flanges, conductors, and line fittings.
- Moreover, low-pressure die casting is instrumental in producing magnesium-aluminum alloy castings for the aerospace industry, including missile casings. Its applications extend to the high-speed railway sector for manufacturing components like sleepers, gearbox housings, contact wire pulleys, and flywheels.
Yontone is a reliable supplier specializing in low-pressure die casting services using aluminum alloy material. Below are aluminum Low Pressure Casting Examples.
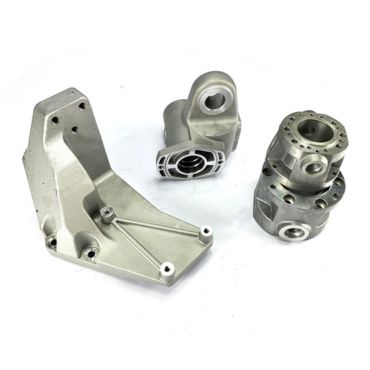
Material: A356,zl102,zl104
Heat Treatment: T6
Surface: Sand blasting
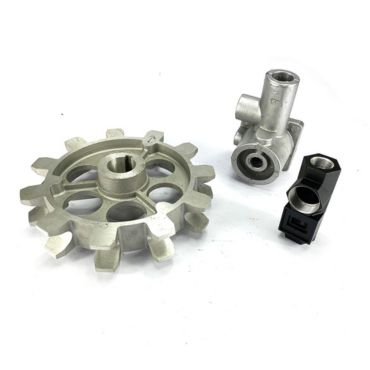
Material: A356,zl102,zl104
Heat Treatment: T6
Surface: Sand blasting
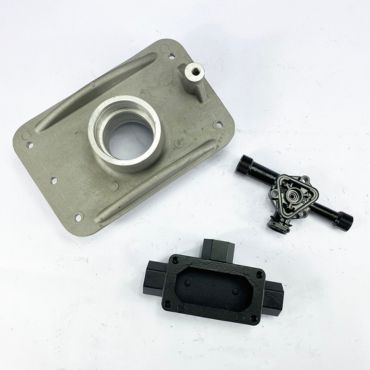
Aluminum Material: A356,zl102,zl104
Heat Treatment: T6
Surface: Sand blasting
Low Pressure Die Casting Processes
The production process of low-pressure die casting includes: mold design, mold flow analysis, sand core design, sand mold production, mold manufacturing, low-pressure casting, shakeout of the product, removal of excess material, heat treatment, surface grinding, sandblasting, and machining.
Yontone has extensive experience in low-pressure die casting production. Feel free to inquire for a quote.
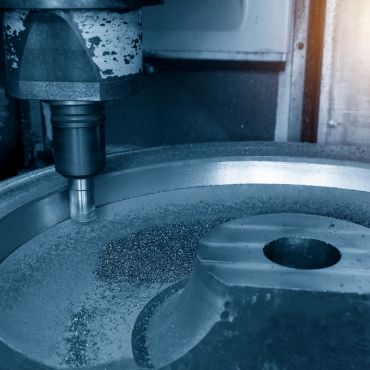
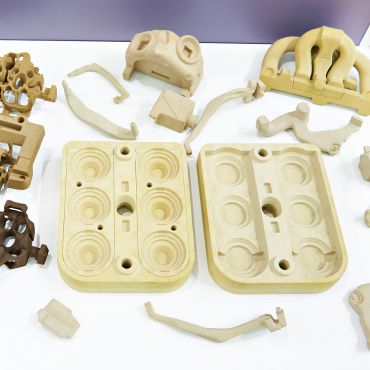
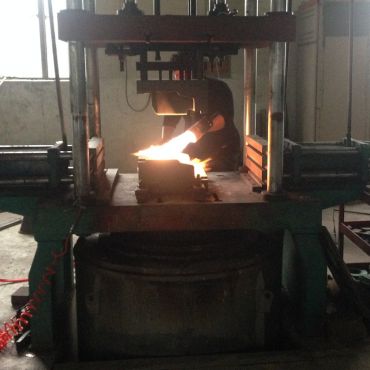
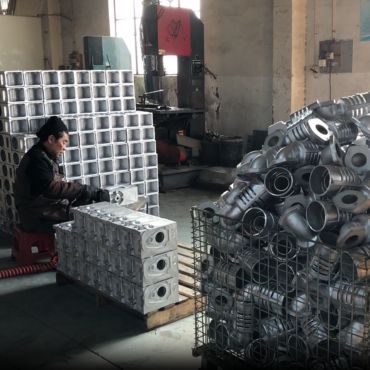
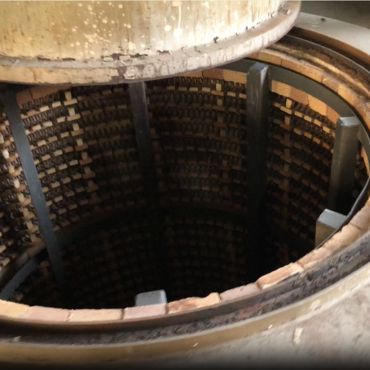
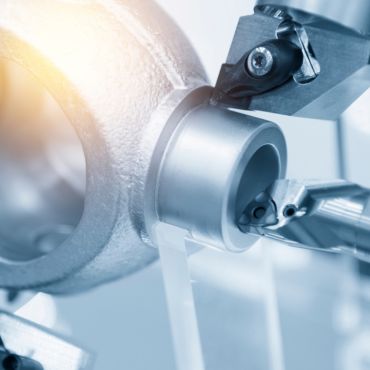
Advantages of Low Pressure Die Casting
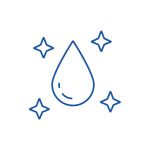
In low-pressure die casting, the molten slag typically floats on the metal’s surface. With metal filling occurring through the riser from the bottom of the holding furnace, low-pressure casting effectively eliminates the possibility of slag entering the mold cavity.
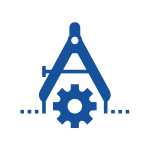
The application of pressure during metal filling enhances metal fluidity, facilitating the formation of castings with dense microstructures, improved mechanical properties, clear contours, and smooth surfaces. This process is particularly advantageous for the molding of large and thin-walled components.
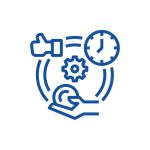
Compared to sand casting and gravity casting, low-pressure casting is more mechanized and demands less manual labor. It can be integrated into automated casting production lines with one operator managing multiple machines or even operating autonomously, resulting in reduced production costs.
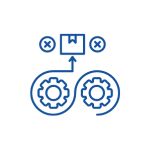
Typically, the need for risers is minimized, and the un-solidified metal in the riser can be recaptured and returned to the crucible for reuse. This greatly increases the metal yield, often achieving rates of 70% or more. Also lead to significant cost savings.
Production Safety of LPDC
Low-pressure die casting’s material feeding and forming processes are entirely machine-driven, resulting in reduced labor intensity and improved working conditions for operators. The equipment is straightforward, and the production process is characterized by high safety standards.
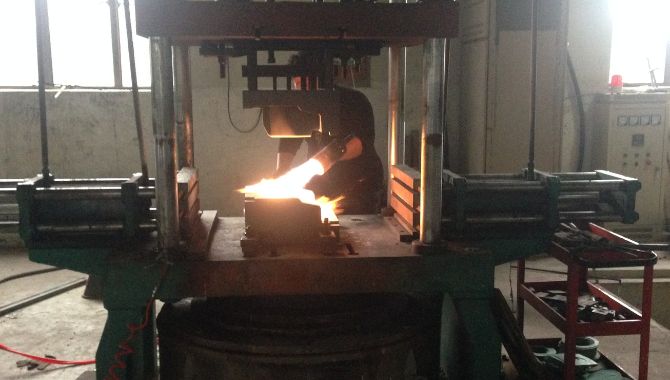
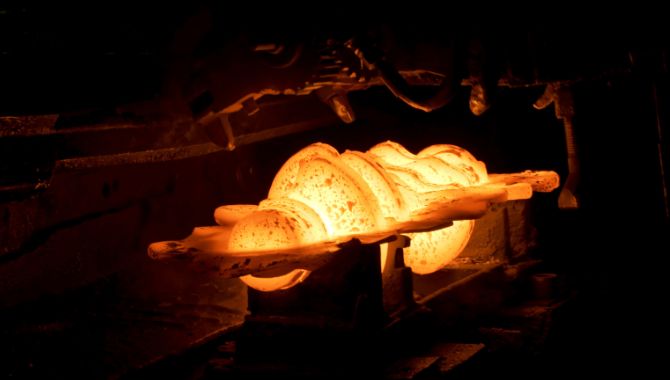
Heat Treatment
The heat treatment process in low-pressure die casting serves not only to increase the hardness and strength of the aluminum castings but also to melt the sand cores inside the castings, cleaning the interior.
Subsequently, shot blasting is employed to clean the surface and internal sand residues of the castings, ensuring a smooth and aesthetically pleasing appearance.
Quality Control
Every finished product undergoes dimensional inspection using three-coordinate measurements.
For products with air-tightness requirements, we conduct X-ray checks after machining.
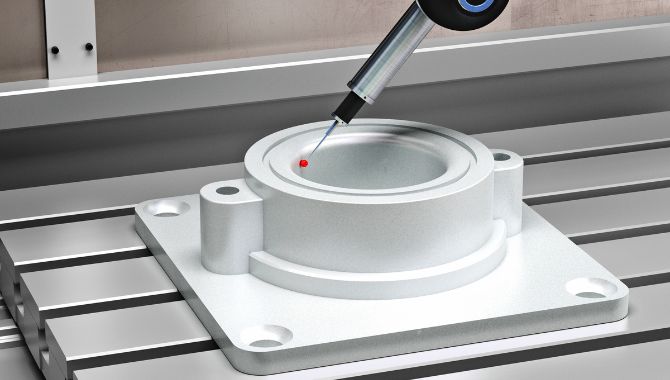
Choose Yontone as Your Low Pressure Die Casting Partner
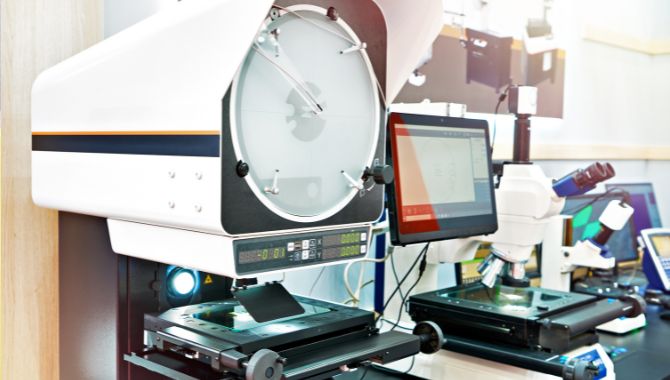
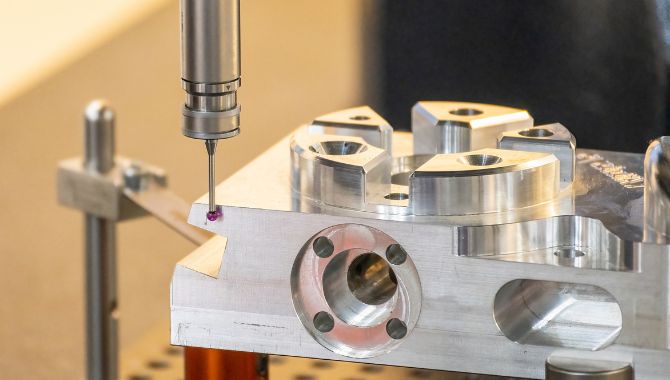
Yontone boasts extensive experience in low-pressure die casting.
- Our mold designers team, with over 8 years of frontline expertise, ensure rational mold design, resulting in high product yields and excellent density with minimal porosity.
- Our production team, excels at adjusting pressure, temperature, and mold-closing times on low-pressure casting machines, consistently enhancing production efficiency.
- We have an in-house heat treatment facility, allowing us to heat-treat our low-pressure die-cast products, making them suitable for machining.
- Our quality assurance reports, encompass heat treatment, material, dimension, strength, and metallographic testing.
- Delivery time, is of utmost importance to us. We maintain real-time communication with our customers via video, phone, email, and photos to update them on production progress. Any technical or process issues are swiftly resolved through video calls, ensuring on-time delivery for every order.
Exceptional mold design, efficient production by skilled employees, minimal product rejection rates, and maximized material utilization all contribute to Yontone’s natural pricing advantage. We don’t engage in price wars; instead, we prioritize product quality and offer cost benefits to our customers, fostering win-win relationships.
As a company with a century-long dream, Yontone’s strength lies in our uniqueness: we stand out where others falter, and we excel where others perform. Our commitment to excellence sets us apart.
Wild Application of Low Pressure Die Casting
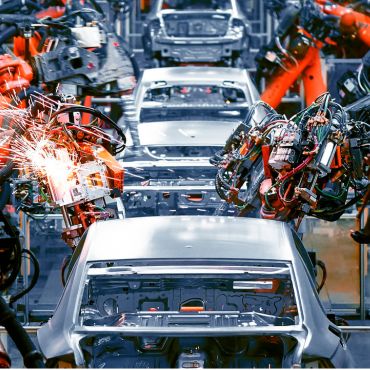
Yontone’s low-pressure die-castings are applied in the Automotive Industry.
Low-pressure casting technology is commonly employed in the manufacturing of automotive components, including engine parts, brake system components, and chassis parts.
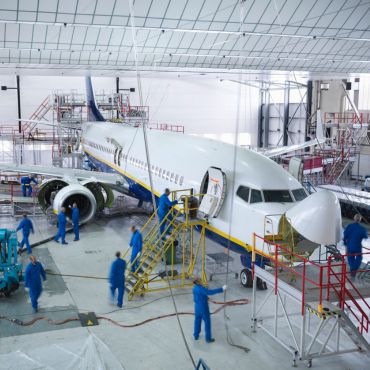
Yontone’s low-pressure die-castings are utilized in the Aerospace Industry.
The extensive use of low-pressure casting in this industry is attributed to its capability to offer higher material density and performance, particularly in the production of aircraft engine components, aerospace structures, and spacecraft parts.
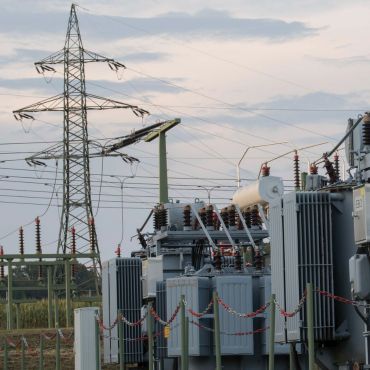
Yontone’s low-pressure die-castings are applied in the Electronics and Electrical Industry.
Low-pressure casting is utilized in the manufacturing of enclosures for electrical equipment, radiators, and other electronic components.
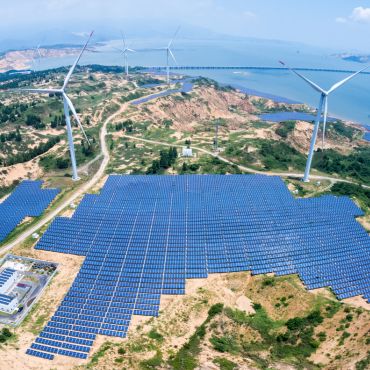
Yontone’s low-pressure die-castings are employed in the Energy Sector.
Low-pressure casting technology is utilized in this sector for the production of critical components in power generation equipment, such as turbines and generators.

Yontone’s low-pressure die-castings are utilized in the Medical Devices sector.
The advantageous features of low-pressure casting, including the ability to produce components with complex shapes and precision structures, make it well-suited for the manufacturing of medical devices and instruments.
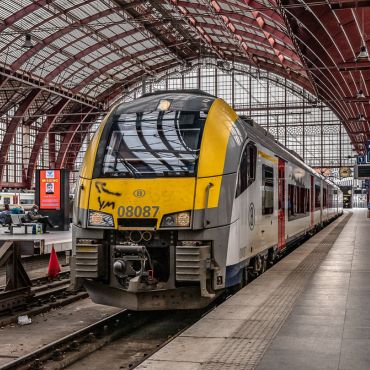
Yontone’s low-pressure die-castings find applications in both Industrial Machinery and General Manufacturing.
Low-pressure casting is employed to manufacture key components of various industrial machinery, enhancing product strength and durability.
Additionally, low-pressure castings have widespread use in general manufacturing, being applied in the production of various parts, components, and industrial products.