With over 35 years of expertise in die-casting mold production, YONTONE excels in tool mold making. Unlike suppliers solely focused on molds, our extensive experience in die casting and machining allows us to create molds with optimized structures and higher production efficiency. We help customers save on production costs while improving efficiency and yield.
Our commitment lies in delivering comprehensive one-stop industrial solutions: from mold design, mold forming, die casting, casting, and machining process design, to surface treatment comparison services for processed products.
The following is the entire production process of the order.
Customers send drawings, we design molds, mold flow analysis, buy mold materials, mold rough machining, heat treatment, mold finishing, EDM, wire cutting WEDM, assembly, drilling, polishing, mold testing, die-casting, machining, surface treatment, packing, shipping
Yontone accept product drawings in both 2D and 3D formats from our customers. For 2D drawings, PDF and CAD formats are preferred. For 3D drawings, we recommend IGS and STP formats. Providing these file types helps streamline the design and manufacturing process, ensuring precision and accuracy in our production.
Designing molds with precision is a crucial step in our process. Yontone meticulously follow your product drawings, taking into account the shrinkage rate for die casting and machining tolerance. This ensures that the final product aligns perfectly with your specifications, meeting the highest standards of quality and accuracy.
Yontone employs advanced CAE (Computer-Aided Engineering) technology software for comprehensive mold analysis. This includes mold flow analysis to assess material flow, pore analysis to evaluate potential defects, and temperature analysis to ensure optimal processing conditions. These simulations enhance our mold design, allowing us to optimize and fine-tune the manufacturing process for superior results.
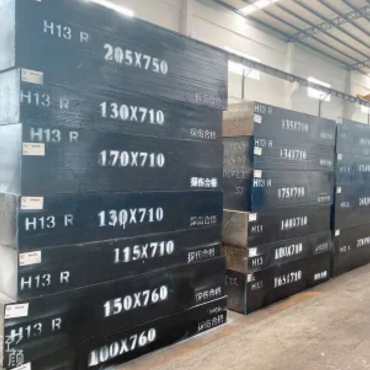
Yontone procures mold materials from various reputable brands, aligning with customer specifications and the desired mold lifespan. Our approach ensures the use of high-quality materials that meet or exceed industry standards, contributing to the longevity and performance of the molds we manufacture.
During the initial machining phase, Yontone conducts preliminary rough machining on the mold cavity. This step involves removing excess material and shaping the cavity to its approximate final form. This rough machining lays the foundation for subsequent precision machining, ensuring the mold progresses toward its final, accurate dimensions.
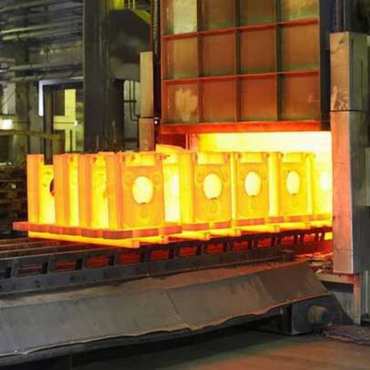
Following the initial processing, the model undergoes a crucial heat treatment phase to achieve a targeted hardness ranging from HRC45 to HRC50. This heat treatment ensures the mold’s durability and resilience, meeting the specific requirements for hardness in the manufacturing process.
After the heat treatment of the mold cavity and subsequent secondary machining, the cavity essentially meets the size requirements specified in the design. This meticulous process ensures that the final dimensions align precisely with the design specifications, achieving the desired accuracy and quality for the mold.
The EDM (Electric Discharge Machining) process is utilized for the mold by employing electric sparks to finish sizes that cannot be achieved through CNC machining alone. This precision technique is instrumental in achieving intricate details and fine dimensions in the mold, ensuring the highest level of accuracy in the final product.
The WEDM (Wire Electric Discharge Machining) process is employed to wire cut holes for pin positioning, specifically for ejection pins within the mold cavity. This precise technique ensures accurate placement and dimensions for essential components within the mold, contributing to the overall functionality and performance of the final product.
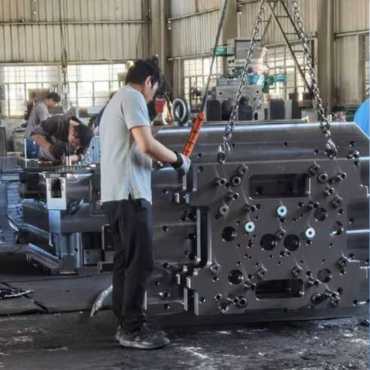
The assembly process involves bringing together the mold frame, mold cavity, slider block, ejection pin, ejection plate, and all associated accessories. This meticulous assembly ensures that all components fit seamlessly, creating a cohesive and functional mold unit ready for the next stages of production.
We utilize an appropriately sized die casting machine to conduct a trial run of the mold. During this phase, we meticulously check the dimensions to ensure accuracy. Subsequently, samples are produced and submitted to the customer for evaluation, allowing for thorough inspection and validation of the mold’s performance against the specified requirements.
Die-casting product production typically involves manufacturing approximately 105% to 110% of the ordered quantity. This allows for any potential defects, and quality control adjustments, and ensures that the final delivered quantity meets the specified order requirements.
CNC turning and milling processes are applied to die casting parts, adhering to the specifications outlined in the 2D drawing with machining tolerance. The initial piece undergoes a full-size checking process, and upon confirmation of meeting requirements, it is submitted for approval. This meticulous approach ensures that the manufactured parts align precisely with the design specifications and quality standards.
Various surface finishing options are available, including but not limited to Powder coating, Painting, Chrome coating, Electrophoresis, Polishing, Brushing, Nickel plating, Titanium plating, and Golden color plating.
These finishes enhance the appearance, durability, and corrosion resistance of die-casting products, providing a range of aesthetic and functional choices based on your specific requirements.
Our standard packaging method typically involves using carton boxes along with pallets, packing belts, and plastic wrap for securing the products. In instances where the parts are heavier, we opt for the use of wooden boxes to ensure secure and reliable packaging during transportation. This approach is designed to safeguard the integrity of the products and minimize the risk of damage throughout the shipping process.