What is Surface Treatment?
Transform the metal surface using both physical and chemical techniques to achieve:
- Alter the performance of the metal surface, encompassing its electrical conductivity, corrosion resistance, and wear resistance;
- Enhance the aesthetic appeal of its appearance, including smoothness, color, and tactile sensation.”
Metal products, such as aluminum alloy die-castings, cast iron products, cast steel products, and brass products, may lack aesthetic appeal and exhibit limited wear resistance, oxidation resistance, and corrosion resistance on their external surfaces if not subjected to surface treatment.
Yontone, under customer requirements, provides metal surface treatment services, involving processing or coating the surface of metal substrates to alter their surface conditions and properties. The choice of surface treatment method varies based on different objectives.
- To enhance aesthetics by changing the color, luster, texture, etc., common methods include polishing, brushing, sandblasting, electroplating, and coating.
- To improve product functionality by imparting new features such as conductivity, thermal conductivity, and wear resistance, common methods include electroplating, coating, and heat treatment.
Metal surface treatment is a crucial process in metal processing, exerting a significant impact on the performance and lifespan of metal products.
Surface Finishing Solutions Offered by Yontone
Common surface treatment methods include Polishing, Plating, Anodizing, Powder Coating, Painting, Electroplating, Passivation, Chemical Conversion Coating, Heat Treatment, Shot Blasting, Electropolishing, Laser Etching
These treatments can be chosen based on the material, intended use, and desired properties of the metal part.
Below are surface treatment services offered by Yontone.
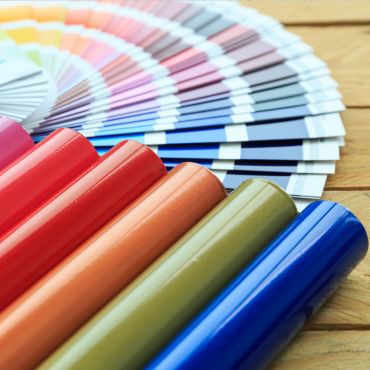
Yontone supplies parts with spray coating (also called, powder coating) treatment.
Spray coating is a metal surface treatment process that involves charging plastic powder through high-pressure electrostatic equipment. Under the influence of an electric field, the coating is sprayed onto the surface of the workpiece. The powder adheres uniformly to the workpiece, forming a powdery coating. After high-temperature baking, the powdery coating flows, levels, and solidifies, creating a final protective coating with varied and distinctive effects as the plastic particles melt into a dense layer. This coating adheres securely to the workpiece surface, achieving both decorative and corrosion-resistant purposes.
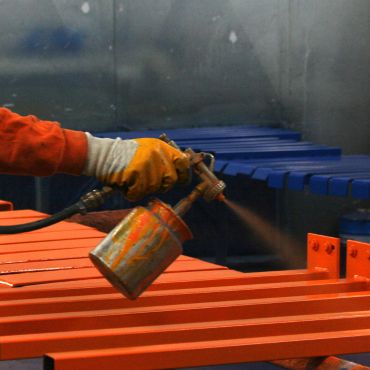
Spray painting is a commonly used surface treatment method, which involves spraying paint onto the surface of a workpiece through a spray gun to form a coating. The principle of spray painting involves using compressed air to atomize the paint into a mist. By adding high-voltage static electricity at the front end of the spray gun, the paint becomes charged. Under the influence of the electric field, the paint is uniformly adsorbed onto the surface of the workpiece, forming a coating. This process is employed to enhance the product’s aesthetics, corrosion resistance, and surface functionality, such as anti-static and anti-slip properties.
Yontone supplies parts with spray paint on almost every metal, aluminum die casting parts, zinc die casting products, brass castings, iron and ductile iron casting parts, and steel casting products.
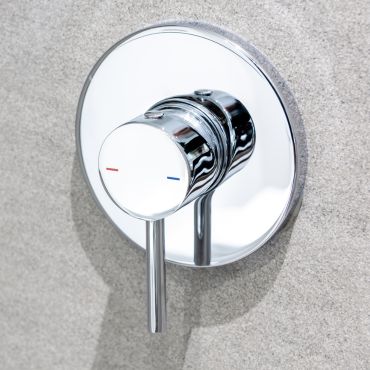
Yontone supplies aluminum alloy die-castings and zinc alloy die-castings with chrome coating.
Chromium plating is an electrochemical process that involves depositing a layer of chromium onto a metal substrate. It uses electrolysis to deposit chromium ions on the cathode, forming a plated layer. Chrom coating is divided into hard chrome and decorative chrome.
- The hard chrome plating process is employed to increase the surface hardness, smoothness, and wear resistance of iron and steel components. This treatment is commonly used in the field of hydraulic components.
- Decorative chrome plating is used in marine engineering & bathroom fittings, with an attractive & corrosion-resistant chrome finish, and protection against environmental factors, moisture & corrosion.

Electrophoresis is an electrochemical process that refers to the phenomenon where charged particles move in a specific direction in a solution under the influence of an electric field. The principle of electrophoresis involves using electrolysis to induce the movement of charged particles in the electric field, achieving purposes such as separation, analysis, and coating of charged particles. Electrophoresis is employed for coating functional films with properties such as conductivity, insulation, and corrosion resistance. It is also used for applying decorative layers to products like automobiles and household appliances.
Yontone offers die-casting parts and castings with electrophoresis.
Yontone offers colorful anodizing on aluminum CNC machining parts, also anodizing on die casting parts and castings.
Anodizing treatment is commonly applied to aluminum alloy surfaces during processing, creating an oxide layer that enhances corrosion resistance and offers a range of color options while simultaneously improving the product’s aesthetic appeal. The principle of anodizing utilizes electrolysis, causing oxidation reactions of the metal or alloy in an electrolyte solution, resulting in the formation of an oxide film. This process enhances the corrosion resistance, hardness, and decorative properties of the workpiece surface.
Yontone provides polishing surface treatment. Polishing can be categorized into mirror polishing, brushed polishing, and regular polishing. Polishing can be applied to various metals, including aluminum casting parts, zinc die-casting parts, brass machining parts, and steel iron castings.
Polishing can make the surface of the workpiece smoother and more even to achieve a glossy or reflective finish, thereby enhancing its aesthetic appeal. It forms a passive film on the surface, thereby improving its corrosion resistance. Polishing metal materials can reduce the grain size of the surface layer, thus increasing its strength and hardness.
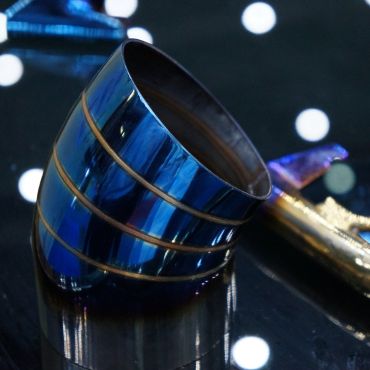
Yontone offers titanium plating service for parts and moulds. Metal materials like aluminum die-casting parts, steel iron castings, and brass machining parts can be titanium-plated.
Titanium plating is an electrochemical process that involves depositing a layer of titanium onto a metal substrate. This method can enhance the corrosion resistance, strength, and hardness of the product’s surface, as well as improve surface functionality. Titanium possesses excellent biocompatibility, and titanium plating can impart new functions to the workpiece surface, such as for use in medical instruments.
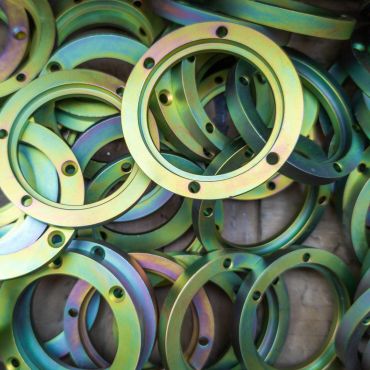
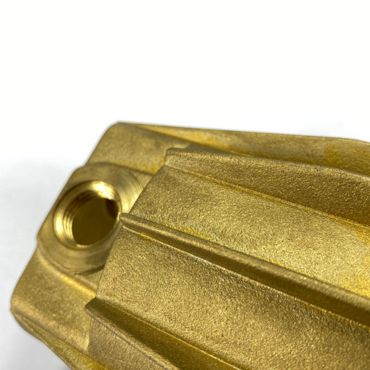
Shot blasting(sand-blasting) is a surface treatment method using high-speed projectiles to impact the surface. It removes impurities, oxidation, rust, deburring, and adherents, and generates indentations, improving the surface roughness, strength, wear resistance, corrosion resistance, and other performance characteristics.
Yontone supplies parts with shot blasting, including aluminum alloy die-castings, zinc alloy die-castings, cast iron, cast steel, and cast copper products. Whether it’s for preparing surfaces for painting or improving the surface quality of metal products, shot blasting is a common and effective surface treatment method.
Advantages of Surface treatment on Metal Parts
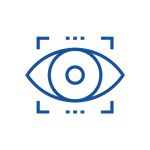
Polishing, electrophoresis, electroplating, and other surface treatments contribute to achieving a sleek and aesthetically pleasing outer surface for metal products.
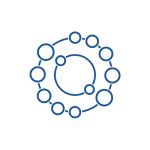
In environments with high humidity or elevated salt levels, metal surfaces are susceptible to corrosion. Our surface treatment methods effectively address these challenges.
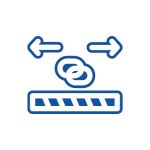
Elevating metal durability, reducing susceptibility to wear, and extending the lifespan of products and components.
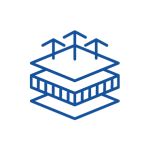
By employing surface treatment techniques, metal conductivity can be altered.
Measurement of Coating Thickness
A film thickness tester is an instrument used to measure the thickness of various coatings. It can be employed to measure coatings on substrates such as metal, plastic, glass, etc., encompassing paints, electroplating, anodizing, ceramics, and more. Widely utilized in the manufacturing of machinery, electronic components, automotive products, and the construction industry. Coatings include anti-corrosion coatings, wear-resistant coatings, conductive coatings, electroplated coatings, insulation coatings, conductive layers, paint coatings, anodized coatings, and others.
Yontone employs different detection methods, such as magnetic sensing, eddy current, infrared, acoustic, and optical, tailored to different substrates and coatings. The objective is to control coating quality and detect defects in the coating.
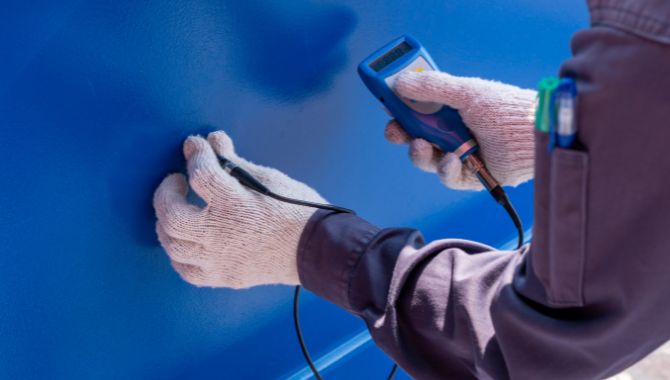
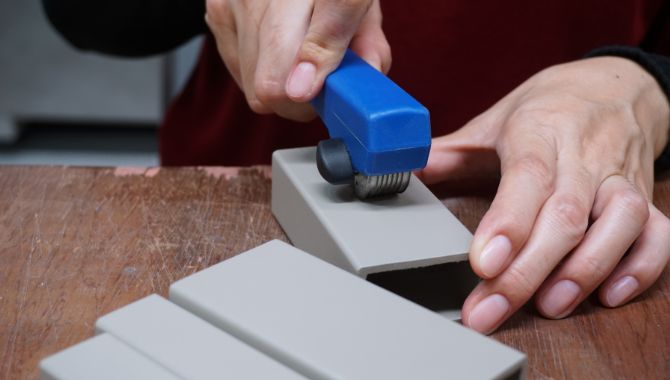
Cross-Cut Test
In addition to the film thickness tester, Yontone also conducts a cross-cut test.
The cross-cut test is an experimental method used to assess the adhesion of coatings. This method involves creating a grid pattern on the coated surface, applying tape to the grid, and then removing the tape to observe the extent of coating detachment, thereby evaluating adhesion. The cross-cut test is a simple, fast, and accurate method for assessing coating adhesion. It is applicable to various types of coatings, including paint, electroplating, anodizing, and is widely employed in industrial production for coating quality control.
Salt Spray Test
Salt spray testing is an environmental test used to assess the corrosion resistance of metal materials or coatings in a salt-laden atmosphere. This type of test simulates salt spray environments found in marine or industrial settings. Salt spray testing can be categorized into two types: natural environmental exposure testing and artificially accelerated simulation of salt spray environment testing. The latter is conducted using a testing apparatus with a specific volume known as a salt spray test chamber. Artificial simulated salt spray tests include neutral salt spray tests, acetic acid salt spray tests, copper salt-accelerated acetic acid salt spray tests, and alternate salt spray tests.
Yontone, following customer requirements or by simulating the intended product usage scenarios, conducts salt spray tests for durations such as 36 hours, 72 hours, or even longer. The purpose is to assess the corrosion resistance of metal materials or coatings, determine the service life of metal materials or coatings, and enhance the corrosion resistance of metal materials or coatings.
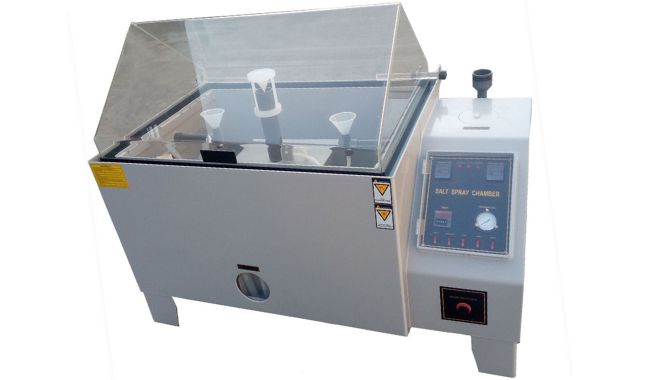
Wild Application Fields of Surface Treatment
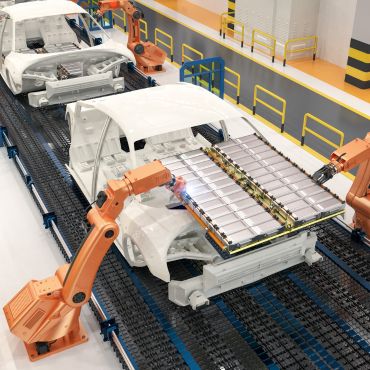
The automotive industry places high demands on the surface treatment of its components. Based on the operating environment and usage, Yontone provides different surface treatments for automotive parts. Vehicles are subject to various corrosion and wear factors during use.
- Electroplating, coatings, and heat treatment can enhance the corrosion resistance of automotive die-cast components.
- Electroplating, coating, and polishing can improve the wear resistance of automotive die casting parts and machined components.
- Surface treatment technologies such as electroplating, coating, and polishing can enhance the decorative aspects of automotive injection-molded products.

The mechanical industry places high demands on surface treatment, addressing issues such as wear during usage, environmental corrosion, and the inherent strength requirements of components. These challenges can be effectively addressed through various surface treatment technologies such as electroplating, spraying, coating, and heat treatment.
Yontone’s die-cast parts and machined products, following appropriate surface treatment, consistently demonstrate outstanding corrosion resistance, wear resistance, and strength in practical use.
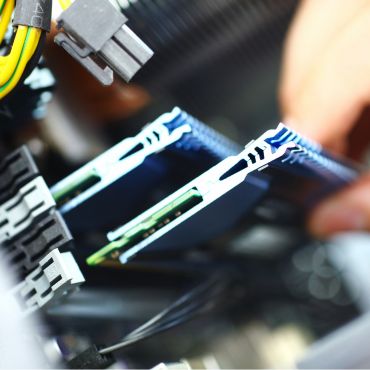
The electronic industry primarily focuses on:
- Conductivity: Surface treatment technologies such as electroplating and coating can enhance the conductivity of electronic components.
- Insulation: Surface treatment technologies like coating and heat treatment can improve the insulation properties of electronic components.
- Corrosion resistance: Electroplating, coating, and other surface treatment technologies can enhance the corrosion resistance of electronic components.
Yontone’s electronic components, after machining and surface treatment, consistently exhibit excellent performance in operation.
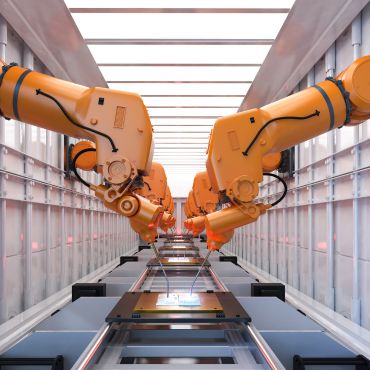
Different industries have varied requirements for surface treatment:
- In the construction industry, there is a need to enhance the corrosion resistance, wear resistance, and decorative properties of building materials.
- The aerospace industry requires improvements in the high-temperature resistance, corrosion resistance, and strength of aerospace vehicles.
- The chemical industry necessitates improvements in the corrosion resistance, wear resistance, and high-temperature resistance of chemical equipment.
Yontone customizes surface treatment for die casting parts and cnc machining products based on the final use and environmental conditions of the customer’s products. This enhances the performance of components and extends their operational lifespan.