What is Aluminum Die Casting?
The main raw material of aluminum alloy die-casting is aluminum alloy ingots. The melted aluminum alloy liquid enters the mold cavity through high pressure and forms fixed-shaped aluminum alloy parts after cooling under pressure.
Modern industry is in great need of this kind of metal suitable for mass production. The aluminum die casting production process of the parts, it has relatively mature production technology and post-processing technology.
Able to create perfect and complex metal parts, the aluminium die-casting process involves the use of a furnace, metal, a die-casting machine, and a mold.
During the aluminum die casting process, some parameters need to be set for the die-casting machine, including: “injection force,” “pressure ratio,” “injection speed,” “mold temperature,” “filling time,” and “holding pressure time.” The setting of these parameters affects the final molding quality of the product.
- Injection force refers to the pressure generated during the die casting process, produced by the pressure pump. The pressure pump transports the molten aluminum alloy solution to the injection piston, which then applies pressure to the metal in the pressure chamber. The pressure applied to the liquid metal is a critical factor in achieving structurally dense and well-defined castings. Therefore, it’s important to understand and control the pressure variations acting on the liquid metal throughout the die casting process.
- Injection speed refers to the speed of the injection head during the die casting process, which can be categorized as slow or fast injection. Generally, slow injection speeds range from 0.1 to 0.5 meters per second, while fast injection speeds range from 0.1 to 1.1 meters per second. Factors that determine the injection speed include the thickness of the casting wall (thinner walls require faster injection), the complexity of the casting shape (more complex shapes require faster injection), the prominence of the casting’s surface (larger prominences require faster injection), and the length of the gating path (longer gating paths require faster injection).
- Pouring temperature refers to the average temperature of the mold during the casting process. Typically, the lowest possible temperature that ensures proper molding and the desired surface quality is used. The casting temperature for aluminum alloys ranges from 650°C to 720°C, with the casting temperature being reduced for alloys with good flowability. For thin-walled and complex castings, a higher casting temperature may be used, while for large molds with good heat dissipation, the casting temperature may be slightly higher.
- Mold temperature refers to the temperature of the mold during the production process. The typical mold temperature for aluminum alloy die casting molds is in the range of 200°C to 280°C. In general, thinner castings and more complex structures require higher mold temperatures.
- Filling time is the time required for the molten aluminum metal to start filling the mold cavity during the die casting process. It typically ranges from 0.01 to 0.1 seconds. The choice of filling time depends on various factors, including the casting’s pouring temperature, mold temperature, the distance of thick-walled sections from the gate, the alloy’s heat of fusion, and the effectiveness of the venting system.
- Holding pressure time, also known as holding time, is the time required for the solidification of the metal in the mold under pressure after it has been filled. Holding pressure helps to crystallize the solid metal under pressure, ensuring that the castings have a dense internal structure. Holding pressure times vary depending on factors such as the alloy’s solidification temperature range, casting thickness (thicker walls require longer holding times), and the size of the casting.
- Cooling time is the duration that the casting remains in the mold. It refers to the time from the start of holding pressure until the casting is ejected from the mold. Adequate cooling time ensures that the casting has fully solidified, cooled, and developed sufficient strength. The goal is to minimize cooling time while preventing deformation and cracking of the casting.
These process parameters are crucial for achieving high-quality aluminum alloy die castings. Companies like Yontone, with their extensive experience, are familiar with these terms and concepts used in die casting and employ them to produce excellent results.
Aluminum Die Casting Parts Applications
Aluminum alloy precision die-casting parts have the characteristics of thin wall, light weight, high strength, high precision, complex shape, smooth surface, good corrosion resistance, strong high-temperature resistance, good thermal conductivity, good mechanical properties, etc., and are used in automobiles, home appliances, rails, etc. It is widely used in transportation, general machinery, shipbuilding, aerospace, and other fields.
Yontone can produce nearly all types of aluminum alloy die-cast components across various industrial sectors. The following are examples of components we have previously manufactured, for your reference.
In the picture, they are Engine Water Pump Housing, Turbo Compressor Housing, Air Brake Systems, Cooling System Turbo Charger, Valve Delete Kit.
They are made of A380 aluminum alloy.
The A380 aluminum die-casting alloy maintains excellent mechanical properties, including strength and hardness, even under high temperatures. The material exhibits superior corrosion resistance and thermal conductivity. In high-temperature environments, it efficiently conducts heat, making it an ideal material for aviation and automotive components.
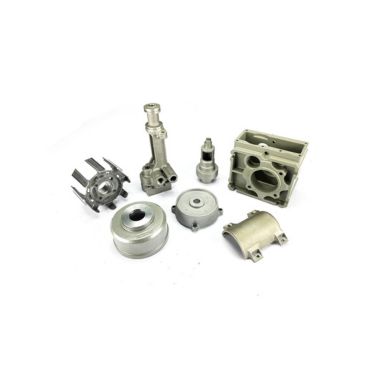
Aluminum die casting diesel engine oil pump housing, connected gear casing, gearbox housing, crankcase, motor engine cover, transmission casting, clutch drum spur sprocket made of AlSi9Cu3.
AlSi9Cu3 is a European standard alloy with notable characteristics, particularly valued for its good creep resistance, a crucial factor for maintaining stability in high-temperature environments. The addition of silicon enhances the overall corrosion resistance of AlSi9Cu3, making it well-suited for challenging environmental conditions. This alloy finds widespread applications in the automotive industry, medical field, and the emerging field of new energy, where its properties are utilized for various components and applications.
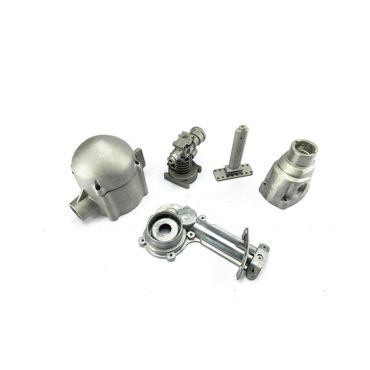
In the picture, they are aluminum die casting auto oil pump, gear housing, and head cover of power tool.
They are made of ADC12.
ADC12 is a commonly used aluminum alloy grade in China, known for its excellent mechanical properties and fluidity. It is capable of producing intricately structured aluminum die-cast components, making it widely applied in the manufacturing of electronic devices and power tools. ADC12 is recognized for its high cost-effectiveness, establishing it as a preferred aluminum alloy material for die casting.
High Pressure Die Casting Aluminum Grades
Aluminum die castings are no longer limited to the automobile industry and instrument industry and have gradually expanded to various other industrial sectors, such as agricultural machinery, machine tool industry, electronics industry, defense industry, computers, medical equipment, clocks, cameras, and daily hardware, etc.
Aluminum die casting parts used in different fields have different material requirements.
As a company that has been in the aluminum die-casting industry for 30 years, Yontone is familiar with the die-casting properties of various aluminum alloy materials, such as:
- Chinese standard GB die-casting aluminum grades: YL101, YL102, YL104, YL112, YL113
The grades of die-cast aluminum according to Japanese JIS standards: ADC1, ADC3, ADC5, ADC6, ADC10, ADC10Z, ADC12, ADC12Z, ADC14. Different materials need to be used according to the product use. - European standard German DIN standard die-cast aluminum alloy materials such as AlSi10Mg, Alsi, AlSi9Cu3, AlSi12Fe,
- American standard ANSI die-cast aluminum alloy materials such as A380 and A356 are also widely used in China.
Aluminum Die Casting Machines and Accessories
Yontone is equipped with state-of-the-art cold chamber die casting machines from top domestic brands such as LK, YIZUMI, and HAITIAN. These excellent machines offer numerous advantages, including high precision, efficiency, consistency, high density, low porosity, superior surface quality, and environmentally friendly material usage.
Through the use of these exceptional die casting machines, Yontone can assist clients in producing high-quality aluminum alloy die-cast products at a lower cost. These products exhibit outstanding material properties and impeccable surface quality while adhering to environmental standards. Our goal is to help clients achieve efficient production and provide them with premium, top-quality die casting parts.
Advantages of Aluminum Die Casting Process
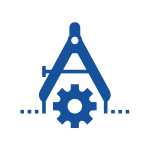
Thanks to our extensive experience in mold design and manufacturing, Yontone’s aluminum die casting parts are known for their exceptional precision.
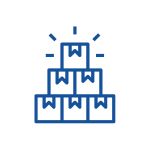
Our highly automated cold chamber aluminum die casting machines, coupled with round-the-clock production capabilities, enable us to achieve exceptionally high production volumes.
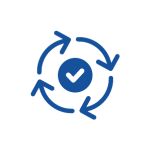
The dimensions of our die-cast products are primarily ensured through the use of precise die casting molds, minimizing the influence of human factors.
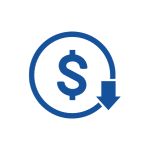
Our automated ladling and extraction machines significantly reduce labor costs and, consequently, lower the unit cost of our aluminum die casting products.
Reverse Engineering
Yontone offers Reverse Engineering Services. Frequently, clients come to us with a physical sample but no technical drawings. In such cases, we employ cutting-edge tools like 3D scanners and other auxiliary equipment to meticulously recreate the product’s dimensions, curves, and shape. These are then documented in both 2D and 3D drawings, serving as the foundation for subsequent mold design and aluminum die casting production. We can repeat your parts accurately.
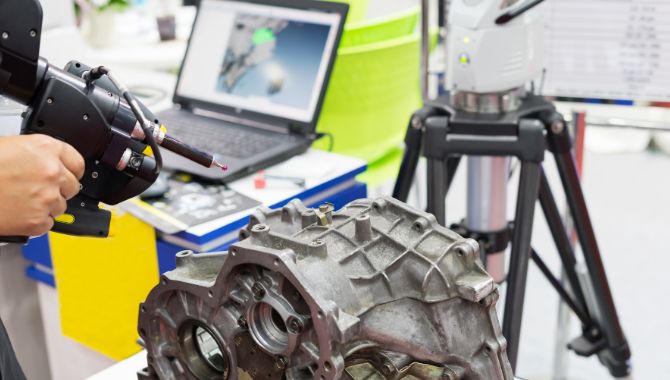
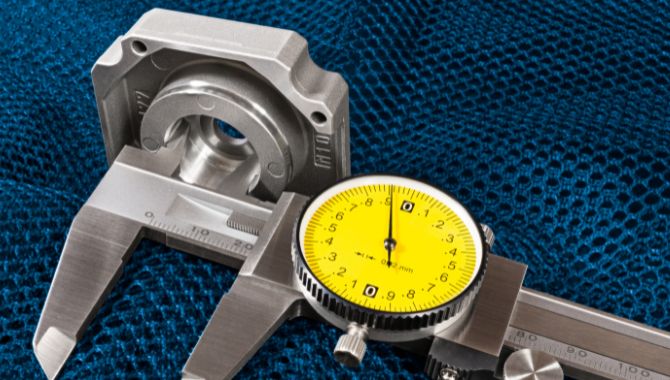
24/7 Continuous Production
Once our engineers configure the die casting machines, our automated aluminum die casting process operates for 24 hours. Every hour, inspectors perform checks on each machine, meticulously examining the size and appearance of the components. This ensures that issues like mold adhesion or pin breakage are swiftly identified and resolved, safeguarding both product quality and mold longevity throughout the automated die casting process.
Quality Control
During each shift, our die casters take the first aluminum die casting part to our QC room for meticulous size checks. Maintaining consistent product dimensions and quality is a priority at Yontone. Before shipment, we also conduct batch sampling inspections as per customer requirements, ensuring that our samples consistently achieve a 100% pass rate.
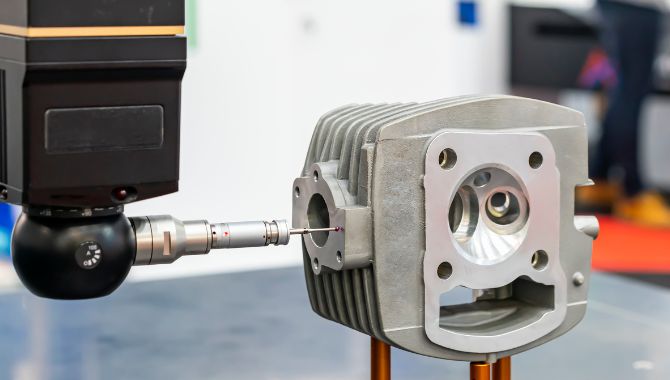
Why Choose Yontone as Your Aluminum Die Casting Supplier?
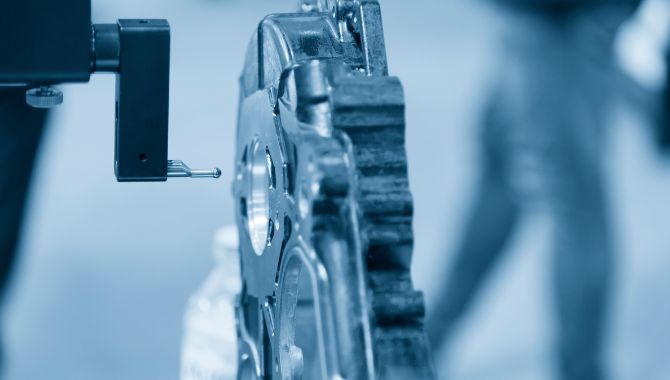
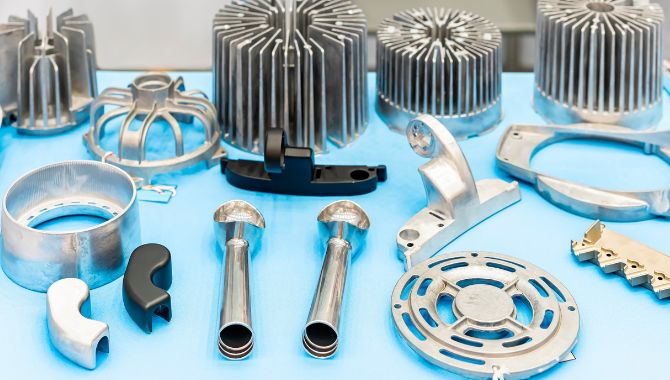
- Technical Team: Our technical team consists of experienced mold design engineers, die casting engineers, and machining engineers with over 8 years of experience. They form project teams for each project, collaborating to optimize mold design and die casting processes. They ensure that there is a reasonable machining allowance for aluminum die-cast products, meeting dimensional requirements without causing porosity issues. Additionally, they design runners and gates efficiently, reducing material weight to save costs while delivering high-quality products.
- Production Workers: Yontone’s die casters have decades of experience in aluminum die casting. They possess in-depth knowledge of the die-casting properties of various aluminum alloys, including setting parameters such as injection speed, pressurization methods, dwell time, automation, and control levels. They continuously adjust these parameters during the casting process to achieve smooth surfaces and precise dimensions. Throughout the process, they self-inspect each product, ensuring product quality from the source.
- Competitive Advantage: Through optimization of molds and product structures, combined with fully automated aluminum die casting equipment, Yontone delivers high-quality products at competitive prices.
- Small MOQ: We understand the challenges faced by small businesses and newcomers to the industry, such as small orders and limited capital. To support our new clients, Yontone offers very low minimum order quantities (MOQ) for initial orders, helping clients start strong and gain a foothold in the market. We are committed to growing together with our clients.
- On-Time Delivery: At Yontone, we prioritize delivering orders on time. We confirm deadlines with clients when orders are placed, and once confirmed, we ensure that the mission is completed as promised.
- Quality Control: Yontone follows a comprehensive quality control process, including regular inspections, scheduled testing, and large-batch sampling inspections before delivery. Our quality reports include size reports, material reports, performance reports, and more.
- Trustworthy Company: With over 35 years of history, Yontone aims to be a company that endures for decades or even centuries. Integrity is the lifeblood of our business, and our responsibility is to provide clients with high-quality products on time.
Wild Application Fields of Aluminum Die Casting Parts
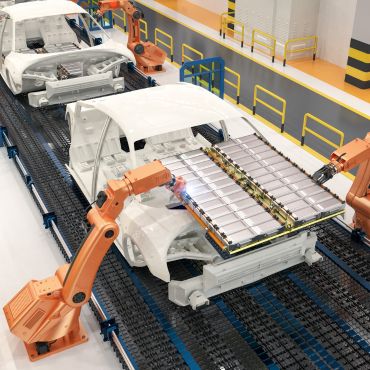
Aluminum alloy die-cast products are lightweight and possess excellent heat dissipation properties, contributing to the reduction of vehicle weight and improved fuel efficiency.
They are commonly used in die-casting the outer casing of electric motors and the heat dissipators for battery compartments in new energy vehicles.
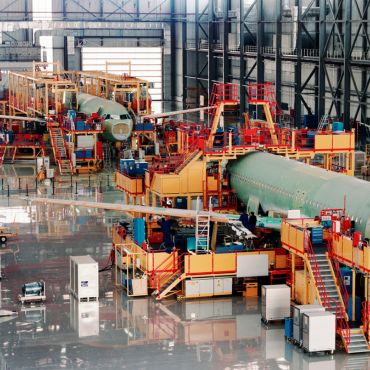
The application of aluminum die-cast products in the aerospace industry plays a crucial role in the structural components of aircraft.
Tail fins and engine housings, which require sufficient strength and heat resistance, benefit from the use of aluminum die-cast components. Additionally, lightweight aluminum die-cast products are employed in interior components such as cabin seats and dashboard elements in aerospace applications.
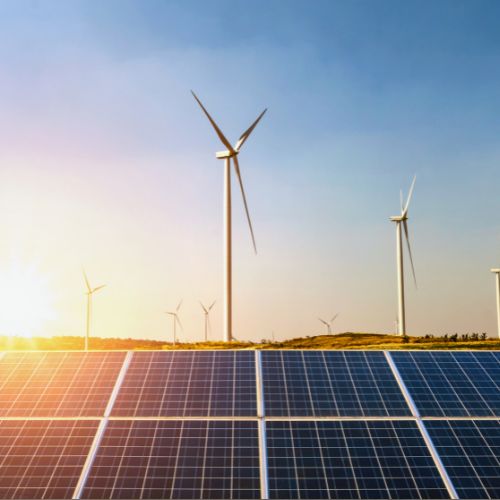
Aluminum alloy die casting finds extensive applications in the renewable energy sector, including the manufacturing of components for wind power and solar energy systems. Key components such as wind turbine bearing supports and generator housings, wind tower bases, solar panel mounts, parts for tracking systems, and inverter casings are all produced through aluminum die casting.
These components offer strength, lightweight characteristics, and corrosion resistance, contributing to the efficiency and durability of renewable energy equipment.
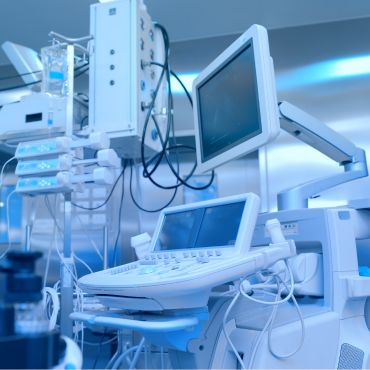
The widespread application of aluminum alloy die-cast components in the field of medical devices is evident. Aluminum die-casting provides lightweight and sturdy casings and supports for medical imaging equipment.
It offers corrosion-resistant instruments for various surgical tools. Portable tools for rehabilitation and auxiliary equipment, such as wheelchairs and canes, are also made using aluminum die-casting. The casings of medical instruments are constructed using aluminum die-cast shells, which are further coated with powder coating for durability and aesthetics. Additionally, aluminum die-cast components play a significant role in the heat dissipation and thermal conductivity aspects of medical equipment.