What is Aluminum Die Casting Mould?
An aluminum alloy die-casting mold, also referred to as a matrix, is a tool employed for casting aluminum alloy products. It is composed of an upper mold and a lower mold, known as the male mold (convex half) and female mold (concave half).
Upon closing the mold, the die-casting machine forcefully injects high-temperature molten aluminum alloy into the mold’s cavity with significant high pressure at high speed. Following a period of pressurization and cooling, the mold’s integrated ejector pin system expels the formed product.
A high-quality aluminum alloy die-casting mold is instrumental in enhancing the quality, surface finish, dimensional accuracy, and production efficiency of aluminum alloy products.
Mold quality hinges on two key factors: mold design and mold production. Collaboration between the mold designer and the mold production department is essential for creating aluminum alloy die-casting molds that exhibit outstanding high precision, extended longevity, and heightened production efficiency.
Aluminum Die Casting Mould Manufacturing Processes
The steps of aluminum alloy die-casting mold making processes are: CNC Milling Process, Heat Treatment, EDM Process, WEDM Process, Polishing, and Assembling
For a more detailed mold manufacturing process, please refer to the “die casting mold” page.
The first step of aluminum die casting mold making: use high speed machining centers to mill the mold cavity, leaving a machining allowance of about one millimeter for the shape of the product. It’s for certain deformation after heat treatment.
After the initial milling, the mold cavity will be sent for heat treatment.
When the cavities come back after heat treatment, secondary machining will be carried out. We call this process fine machining. This time, all sizes are according to the mould design drawing pdf.
After two times of machining, there are still some areas difficult to cut by high-speed cutting, then they will be completed by EDM.
There are many deep grooves and narrow slits and complex cavities on the mold surface, which are difficult to process with milling machines. This requires EDM electric discharge machining.
In addition, EDM is also commonly used for some parts that require particularly high processing accuracy and surface roughness.
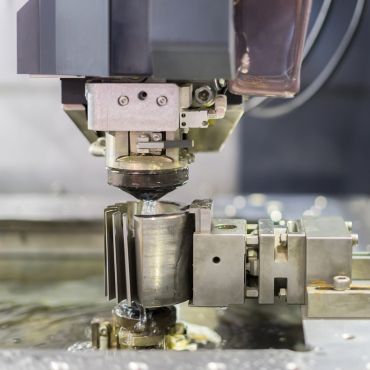
The working principle of WEDM (wire cutting) is to use a continuously moving thin metal wire (called an electrode wire) as an electrode to perform pulse spark discharge on the workpiece to remove the metal and cut it into shape.
The ejector holes in the mold, as well as some sharp-angled, special-shaped holes that cannot be machined, and accessories are all completed by wire cutting.
After this process, mold cavity will be polished. And last process, assemble the aluminum die casting mold, and trial-out.
Aluminum Die Casting Moulds for Different Use
Aluminum die-casting molds find extensive applications in various fields, including auto parts, motor housing, electric tools, lamps, pots, tableware, furniture, elevator parts, and a wide range of housings.
- Auto parts and power tool molds require higher precision and surface finish due to larger production volumes, longer mold lifetimes, and increased durability demands.
- On the other hand, molds for lamps and furniture accessories may not demand high external dimensional accuracy but place a strong emphasis on the aesthetic appearance.
Advantages of Aluminum Die Casting Mould
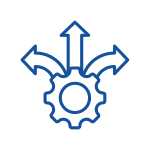
For products that cannot be achieved by machining and stamping, aluminum alloy die-casting molds can be made in one piece.
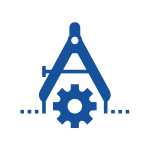
Products produced by aluminum alloy die-casting molds have stable dimensions, and high precision, and are convenient for follow-up machining.
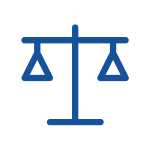
Aluminum alloy die-casting molds can be produced 24 hours a day, which greatly improves the efficiency of mass production.
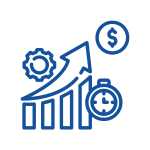
Aluminum alloy products produced by die-casting molds are low-cost compared with machining, and even if they are scrapped, they can be recycled and reused.
In-house Mould Design
The client provides the 3D drawings or physical samples of the product, and the designer will do CAD and CAE design, then use the verification of the mold flow analysis, and finally send the 3D model of the Aluminum Die Casting Mold to the customer for confirmation.
The rationality of the aluminum die casting mold design, including the parting surface, flow channel, feed port, ejector pin position, etc.
In the design of the product, there are places that need to be strengthened, and ribs need to be added.
For positions with extremely thick walls, it is necessary to increase exhaust and slag bags to prevent air holes in the product wall due to the lack of gas removal, air holes appear on the assembly surface after machining, which will cause the product to be scrapped.
Similarly, when estimating the machining allowance of the product, the proportion should also be calculated reasonably.
The shrinkage rate of aluminum alloy is different from that of other metals and needs special calculation.

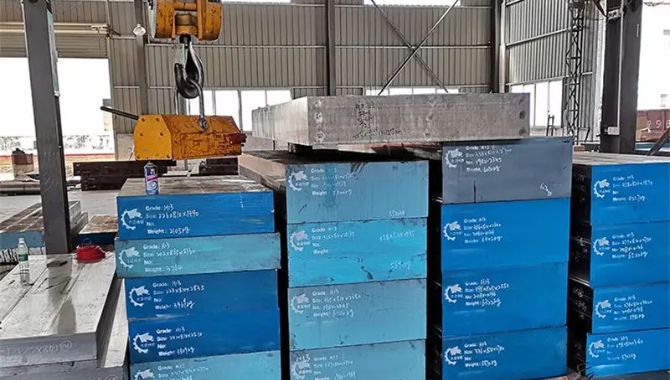
Durable Mould Material
For molds with large output and life expectancy above 10w-20w, we will use: 8418, 8407, 8433, LG, DAC-MAGIC, Dievar and other core materials for professional heat treatment to improve the hardness and toughness of the core. Therefore, the erosion resistance, crack resistance, thermal wear resistance, and thermal strength of the mold core can finally achieve the purpose of improving the service life of the mold.
Standard Die Casting Mold Frames
The use of standard mold frames, and conventional mold frames, we will use CNC milling, or sand casting.
Depending on budget and mold requirements. The precision of the standard mold frame is higher, and the price is also higher, but if the customer intends to continue production with a replacement core, the matching degree of the standard mold frame will be better. Calculated, in fact, the standard mold frame is actually very cost-effective for products with a large enough number of products and high requirements.
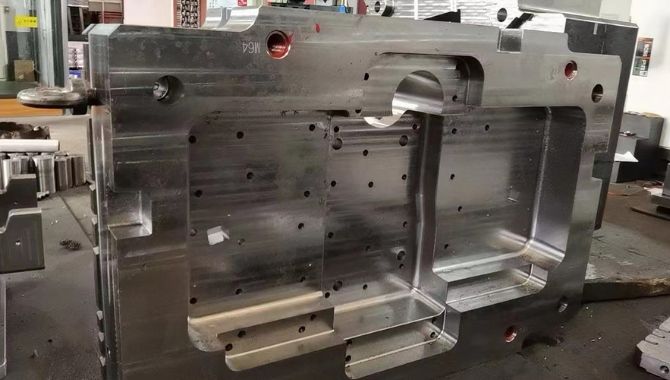

Hydraulic Die Spotting Press
With the widespread application of integrated aluminum die-casting, the sizes of products and molds are getting larger and larger, making it impossible to manually match molds.
Yontone cooperates with the mold spotting machine to assemble the mold, coupled with seasoned workers, after the mold is clamped and opened, the product fits perfectly, the parting line is not obvious, and there are few parting line burrs.
The matching of the mold is very important. If the upper and lower molds are well matched, the life of the mold will be extended by 5%-10% on the original basis.
Reliable Aluminum Die Casting Mold Supplier
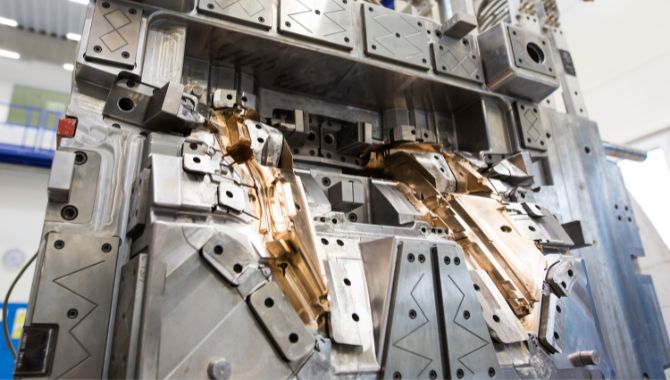
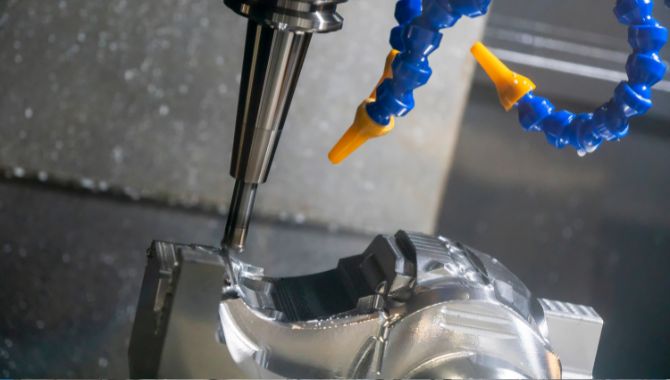
Yontone company has been engaged in the design and production of aluminum alloy die-casting molds for nearly 40 years. The engineers have rich experience in aluminum alloy die-casting. The engineers have more than 8 years of experience in mold design and are familiar with the aluminum alloy die-casting process and machining process. We will give full play to the advantages of Yontone’s one-stop die-casting supplier, and design aluminum alloy die-casting molds with high efficiency, high precision, long life, and low price to help your aluminum alloy die-casting business.
- Automation: The molds we designed have high production efficiency and smooth demoulding. They are not only suitable for manual-operated die-casting machines but also suitable for automation-line die-casting in die-casting factories equipped with automatic robotic arms for picking parts.
- Guaranteed material quality: Choose certified high-quality mold steel materials.
For example, H13 materials with the same composition can have a difference of up to $1.00-3.00/kg per in the domestic market in China, you can imagine the difference in quality between molds made of such materials. Yontone will use verified steel with higher strength and toughness, making the mold more durable and longer life. Ensuring the lifetime of the mold, and controlling the price and cost of the mold. - Generally speaking, the price of a pair of molds ranges from thousands to hundreds of thousands of dollars. There are reasons for being expensive, and there are reasons for being cheap. According to the customer’s product structure, order quantity, and precision requirements, Yontone will recommend suitable mold materials, hoping to provide customers with the most cost-effective aluminum alloy die-casting molds within a reasonable price range. Make sure that it is worth every penny spent by customers.
- Short lead time: Regular mold lead time is 25-55 days after confirmation of the mold design drawing. Urgent molds can be delivered within 20-35 days after drawings are confirmed. Solve customer lead-time problems.
- Mission: With decades of experience in design and production, Yontone not only provides high-quality, reasonably priced aluminum alloy die-casting molds for large, medium-sized, and small-sized enterprises, but also provides technical support such as aluminum alloy die-casting parameter setting and pressure adjustment for new die-casting companies. . We are not a pure aluminum alloy die-casting mould supplier, but also your partner in die-casting production.
Wild Application Fields of Aluminum Die Casting Moulds
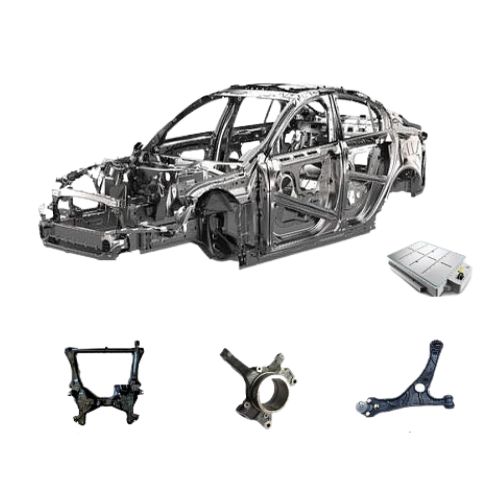
As the demand for lightweight and integration of automobiles intensifies, the materials of more and more components have changed from iron to aluminum alloy. Therefore, in the auto parts industry, aluminum die-casting molds are booming.
The main components include power system, steering system, chassis, suspension system, pumps, clutch housing, shock tower, etc.
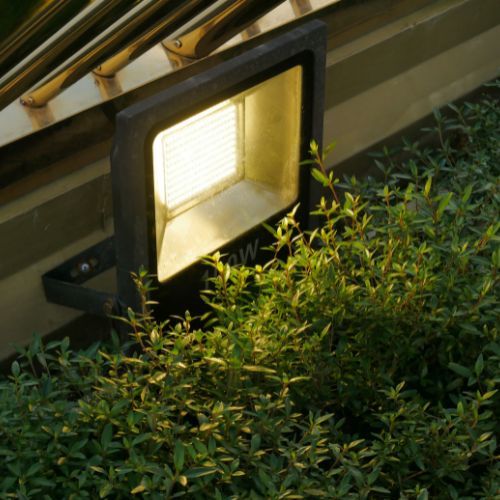
- Aluminum alloy material has a high thermal conductivity, which can effectively conduct the heat generated by the LED lamp to the surface of the lamp body and dissipate it, which can greatly extend the service life of the LED light source.
- At the same time, aluminum alloy materials have the characteristics of light weight and high strength.
- Through surface treatment, it can also have good corrosion resistance.
- The cost is also lower than stainless steel and iron, so most lamp casings are now produced through aluminum alloy die-casting molds.
Yontone has more than 30 years of experience in the design and production of aluminum alloy die-cast lamp housing molds and is dedicated to serving you.
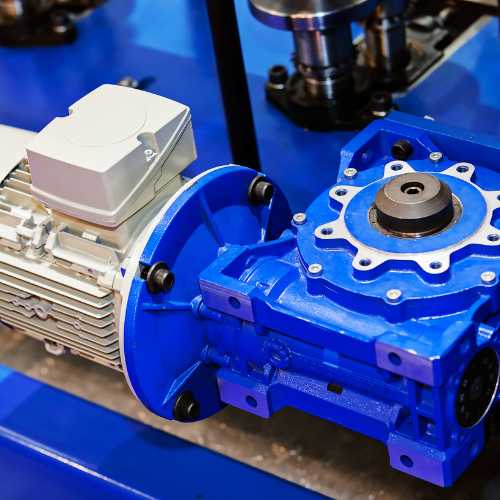
Various industrial motors, gearboxes, and power tools all choose to use aluminum alloy die-casting for their casings because aluminum alloy is lighter than iron and more durable than plastic. It can also be recycled.
Yontone has helped customers design and produce many gearbox housing power tool housing, and industrial motor housing aluminum die casting molds. The product quality and cost performance are very high.
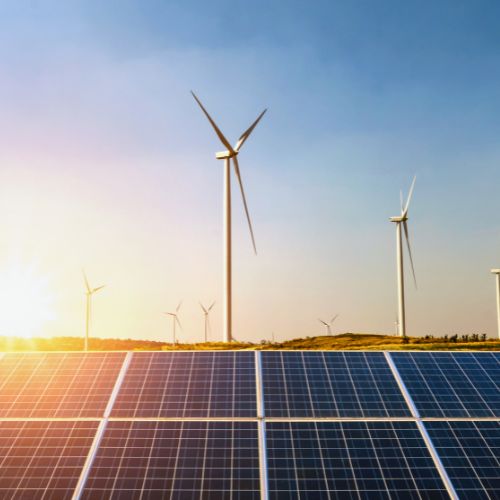
In the solar energy industry, wind power energy, and other new energy industries, aluminum die casting parts are widely used.
Yontone has experience in making aluminum die casting moulds for turbines, generators, and pump components. Blades, hubs, shafts, gears, frames, mounting brackets, electrical connectors, pumps, gears, drill bits, valves, and casing components.
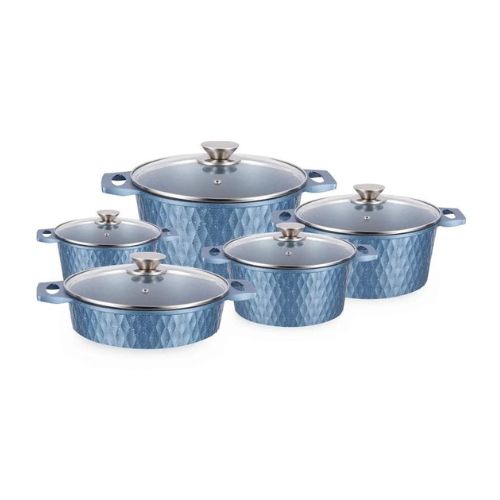
Die-cast pots are non-stick pots produced by the die-casting process. Compared with other technologies:
- The surface is smoother, which can reduce or avoid secondary mechanical processing.
- The production speed is fast and the strength and quality are better.
- Aluminum die-cast pots are lighter than iron pots and more durable than stretched aluminum pots.
- It is cost-effective and can be made into various woks, pans, barbecue pots, and frying pans through aluminum die-casting.
- Many color patterns can be made through different surface treatments, such as Teflon coating, spray paint, etc.
Yontone manufactures many different types of high quality aluminum die casting cookware molds for clients all around the world.

Aluminum die castings can be used in some medical products, such as surgical instruments, medical instruments, medical device parts, etc. The excellent electrical conductivity and heat dissipation properties of aluminum alloy make it suitable for medical devices such as electrical scalpels and medical high-frequency electrodes. At the same time, aluminum alloys can also be used to make parts for medical equipment such as medical bridges, operating beds, and wheelchairs.
Yontone manufactures aluminum die-casting molds for medical device parts, producing countless high-quality medical devices.