What is die casting?
Die casting is a process to form material ingot into the shape you designed.
- Using an electric furnace or centralized melting furnace, turn metal ingot into metal liquid
- Using a die casting machine, with high speed and high pressure, to feed the metal liquid into a steel permanent mold
- After a period (calculated by the engineer), the product is cooled and formed. Eject the parts from the machine.
Die Casting Parts with Different Materials
Die casting is a complex process that requires both good die design and good die casting process design. Yontone can do both.
Here is a simplified overview of the die casting process:
- The molten metal is injected into the die cavity through a runner and gate system.
- The metal solidifies and the casting is formed.
- The casting is ejected from the die and the process repeats.
The gate is a critical component of the die casting process. It accelerates the flow of metal into the cavity and makes it easy to separate the runner from the casting.
Yontone has extensive experience in designing and manufacturing die casting dies and processes for a variety of materials, including aluminum alloy, zinc alloy, copper alloy, and magnesium alloy.
Below are some die casting parts that Yontone has made for reference:
Aluminum alloy and magnesium alloy are two common materials of cold chamber die casting.
The picture shows some aluminum alloy die casting products, including mower housing, power tool parts, transmission box, water pump, bevel slide miter saw upper guard housing and safety cover.
These products are eventually assembled, so they all need to be machined after the aluminum die casting process. Surface treatment is also required, but it must be done before machining. Therefore, it is important to protect the surface during CNC machining. These products are all appearance parts, so they must be free of scratches.
Magnesium alloy is lighter than aluminum alloy, its tensile strength and fatigue strength are not as good as aluminum alloy. It is also easy to oxidize, and magnesium alloy powder is flammable, the production process is dangerous. Therefore, most products are now produced by aluminum die casting. The cost and performance are optimal.
Zinc alloy die casting is typically produced using a hot chamber die casting machine. This is because hot chamber die casting machines are more efficient and cost-effective than cold chamber die casting machines.
The picture shows zinc alloy die casting products, including door hinges, radiator trim panels, parking meter housings, integrated power modules, marine hardware, and evaporator line base plates.
Zinc alloy has a density that is nearly 2.5 times that of aluminum. It has good casting properties and can be used to produce complex, thin-walled precision parts with smooth surfaces. It has a low melting point of 385℃ and is easy to die cast. Zinc alloy die casting products can be subjected to a variety of surface treatments, such as chrome plating, electroplating, electroless nickel plating, painting, and spraying. Zinc alloy is corrosion-resistant, so it is a popular choice for marine parts, door handles, and bathroom faucets and handles.
Commonly used 59 brass has a die casting temperature of 900-1020°C. Brass has good electrical conductivity, corrosion resistance, strength, and hardness. Die casting can produce brass products with higher precision than sand casting. The pictures show a pool bottom lamp shell, a juicer knob, and a handle. Brass has good mechanical properties and wear resistance, and can also be used to manufacture precision instruments, ship parts, gun and shell casings, and coins.
Brass alloy die casting has a high die casting temperature, and the service life of the mold is far less than that of aluminum alloy die casting. High die casting temperatures can cause brass die casting molds to crack, making it difficult to demold and affecting product appearance. Therefore, regular maintenance is essential.
The price and density of copper materials are also high. Therefore, copper die casting is relatively expensive overall and is suitable for high-end products.
More High Pressure Die Casting Parts
Die casting parts can be used in different industries: automotive, medical, aerospace, electronics, telecommunications, energy, new energy, marine, power tools, power systems, etc.
Yontone is an OEM die casting manufacturing company, every part can be customized, we accept drawings for production, and also samples for reverse designing.
Die Casting Machine and It's Accessories
Die casting machines are divided into hot chamber and cold chamber types. The key difference is whether the injection system is immersed in the molten metal.
Hot chamber die casting machines are typically used to cast zinc alloys, while cold chamber die casting machines can be used to cast a wider range of alloys, including aluminum, copper, magnesium, and zinc.
Die casting machines are the main equipment in a die casting unit. Other equipment includes auxiliary machines, furnaces, mold temperature controllers, pick-up robots, spray robots, die-spray packages, multi-link automatic ladles, foundry plus robots for extracting, trim presses, molten material handlers, etc.
Yontone’s die-casting workshop is equipped with the most advanced robotic automation equipment, including mechanical robotic arms and automatic transmit systems. This helps to reduce labor costs and improve production efficiency.
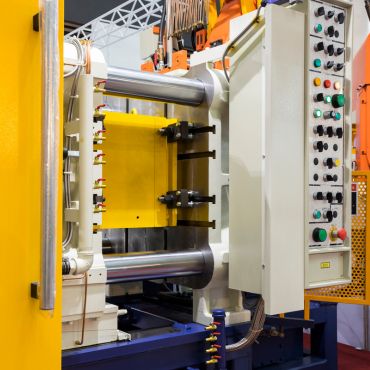
Mainly used for aluminum die casting, magnesium alloy die casting and brass die casting. Sometimes, zinc die casting parts can be die casted in cold chamber die casting machines too.
Yontone supplies die casting parts made by 280ton-2000ton die-casting machines.
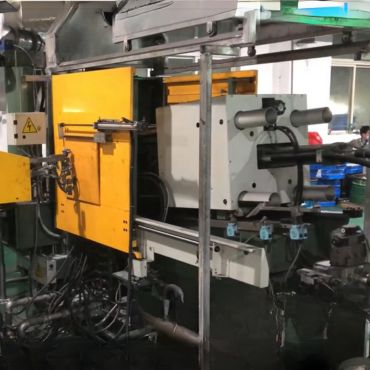
Hot Chamber Die Casting Machine only used for zinc die casting process.
Yontone manufactures zinc die casting parts with 88ton to 400ton hot chamber die casting machines.
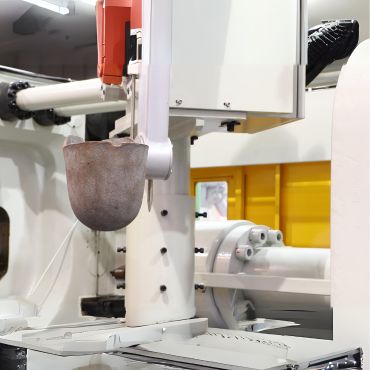
Yontone uses robotic automation ladles and pours to automate the transfer and pouring of molten metal into the cylinder of die casting machines. This allows for 24/7 production, which has significantly improved productivity and reduced production costs.
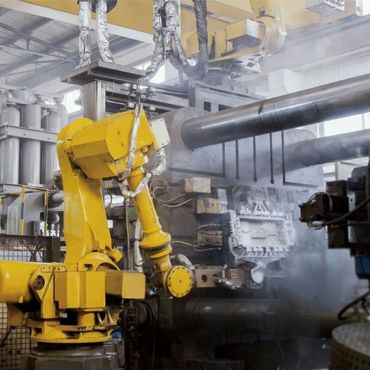
Yontone uses Automatic Extractor Machine Industrial Robot Arm to automatically remove die castings from die casting machines. This has helped to reduce labor costs, improve efficiency, and achieve 24/7 production.
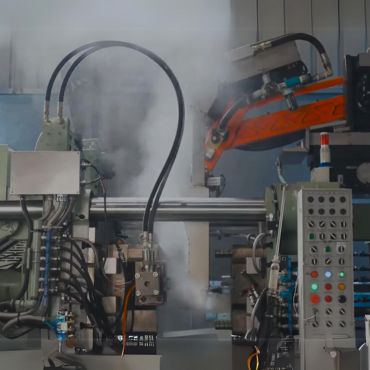
A robotic die lube spray system is a system that uses a robotic arm to automatically spray lubricant onto the molds of a die casting machine. This type of system is often used in high-volume production environments to improve productivity and reduce costs.
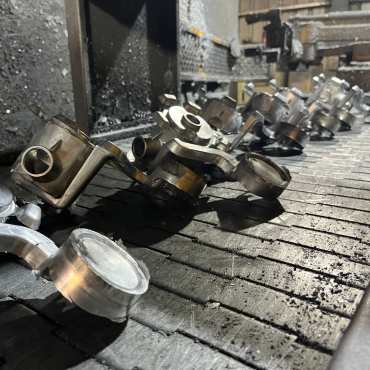
The automatic metal conveyor belt, together with the automatic extractor machine industrial robot arm, transfers the finished casting products to the deburring and packaging department, improving the efficiency of the assembly line.
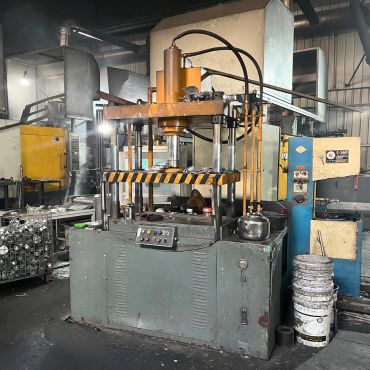
A trimming machine for die casting parts is a machine that is used to remove excess material from die casting parts. This process is necessary to ensure that the parts meet the required specifications and to improve their appearance.
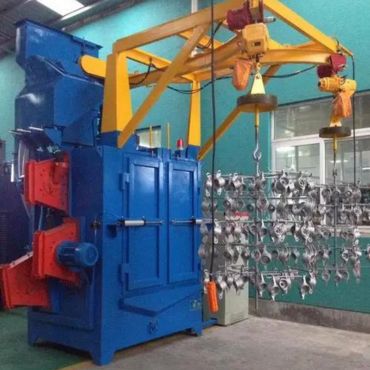
Shot blasting machines use high-speed rotating nozzles to propel steel or iron shot against the surface of die casting part, cleaning and strengthening it. Shot-blasted parts have a uniform metallic sheen, which can improve product appearance. They also deburr the surface and increase surface adhesion, which is often necessary before surface treatment.
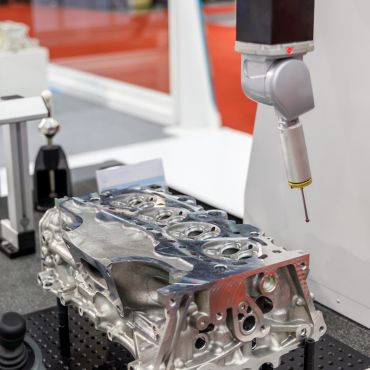
A CMM checking machine, also known as a coordinate measuring machine, is a device used to measure the dimensions of objects with high precision.
Yontone will use CMM checking machines to randomly inspect die castings and generate full-size reports.
Advantages of Die Casting Process
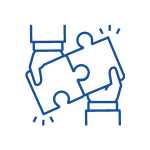
Through continuous improvement of mould design, many parts can be integrated into one product, which reduces the subsequent assembly and machining process and saves a lot of costs.
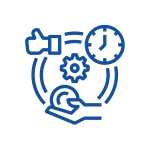
With the addition of an automatic robot arm, die-casting equipment can achieve 365 days, and 24 hours of uninterrupted production, greatly improving production efficiency.
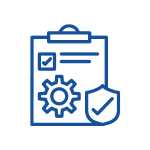
Compared with sand casting, gravity casting, and low-pressure casting, die casting has more stable overall dimensions and better air tightness.

Die-casting products, like aluminum alloy and zinc alloy, magnesium alloy die casting parts are much lighter than steel products, which is very suitable for automotive and aviation industrial.
Self-Designed Die Casting Mould
Yontone has rich experience in mold design and production. The mold we designed is reasonable in structure and high in production efficiency. A good mold can produce a good quality product.


Seasoned Die Casting Engineer
Die casting process designers have more than 15 years of die casting experience. The die-casting parameters are set to achieve the best die-casting product effect.
Quality Control
Our quality control starts from mould size, before die casting, we will use CMM to check the critical size in the mould cavity. Which will assure the size of die casting parts.
After die casting, as the final use of the parts and the requirement from the customer, we will check size, strength, porosity, etc.
A full set of the checking documents and material certification will be sent to the customer along with the cargo.
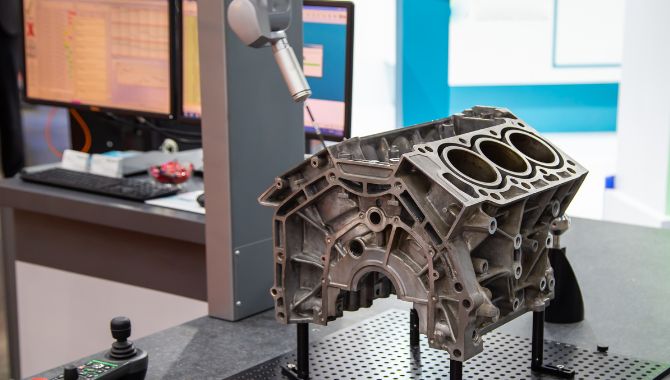
Why Choose Yontone to Be Your Die Casting Parts Manufacturer?
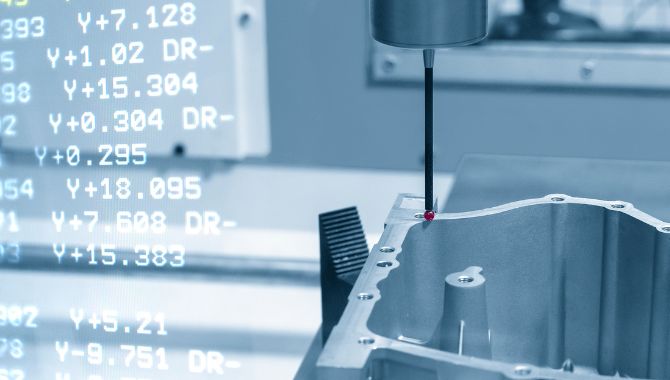
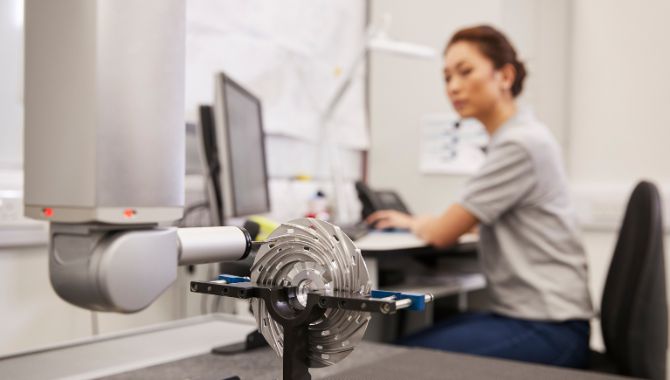
Yontone is a one-stop solution provider for die casting, with almost four decades of experience in die casting, mold making, and nearly two decades of experience in CNC machining.
Our extensive production experience in die casting, mold design, and machining forms a positive cycle, enabling us to design better molds, optimize the die casting process, and ensure that products can be better machined into finished products.
- We have a team of engineers with at least eight years of experience in fixture, cutter, and tooling design.
- With over 35 years of experience in mold making and die casting, we have accumulated a wealth of experience in design and production.
- Equipped with advanced hot chamber and cold chamber die casting machines, Yontone can die cast aluminum, zinc, brass, and magnesium alloys.
- During the production process, we conduct self-inspection and additional inspection to ensure that no defective products are produced.
- Performance testing reports, material certifications, full-size checking documents, and other documentation requested by the customer are provided prior to shipment, subject to customer approval.
- Ship on time
- Offer small MOQs
- Competitive prices.
Yontone is trusted by more than 100 customers from 15 countries, and integrity is more important to us than life. We will always fulfill our promises, whether in terms of quality or delivery.
Wild Application Fields of Die Casting Parts
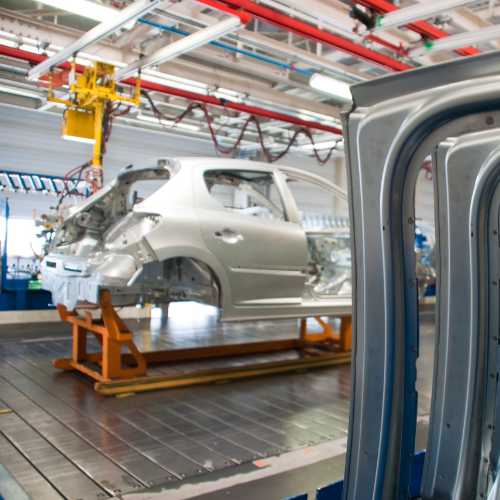
Die casting can achieve product shapes and sizes that cannot be achieved by stamping and machining. Die casting is widely used in the automotive, motorcycle, and aviation industries.
Specifically, there are:
Aircraft field: instrument panel, display, control panel, etc., engine casing, engine blades, fans, and other fuselage structural parts, wing structural parts, landing gear, etc.;
Motorcycle field: engine block, cylinder head, crankcase, transmission Box housings, clutch housings, etc., frame and suspension system components, fuel tanks, fenders, rearview mirrors, etc.;
Automotive field: engine block, cylinder head, crankcase, gearbox housing, clutch housing, body structural parts, suspension system components, braking system components, instrument panels, seats, door panels, door hinge, bumper, bumper bracket, wheel hub, alternator cover, transformer shell, battery box, cooling fan, radiator, transmission housing
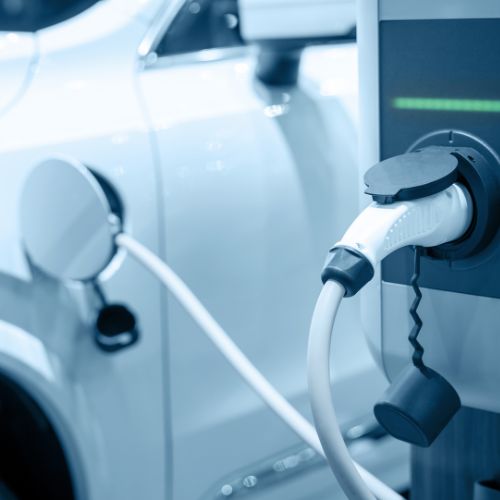
With the rise of new energy vehicles, a large part of the production capacity of die castings is used in this field.
Now, many automobile and motorcycle parts are integrated through design and manufactured by die casting to generate integrated parts, reduce the cost of manual assembly, and reduce assembly errors. Especially for new energy vehicle die-casting components, such as large battery shells, battery covers, battery connectors, charger shells, charging sockets, and integrated body and frame.
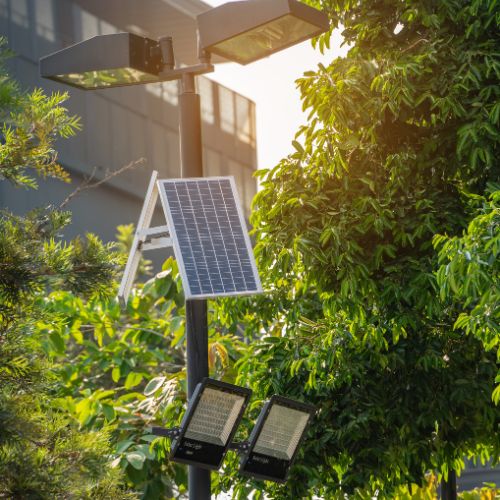
Die casting is a relatively low-cost production process that provides efficient, large-scale, and lightweight light housings for lamp manufacturing.
Die-cast lamp housings that have undergone surface treatment such as spraying are beautiful, waterproof, and durable. Die-cast lamp housings are highly accurate, variable in shape, strong, and easy to assemble. They can achieve IP65 or higher waterproof performance through the result of the sealing ring.
Various types of lamp housings, such as solar street light housings, floodlight housings, garden lamp housings, and factory lamp housings, as well as various heat sinks, heat sinks, lamp heads, lamp holders, and lamp shades that are commonly used on lamps.
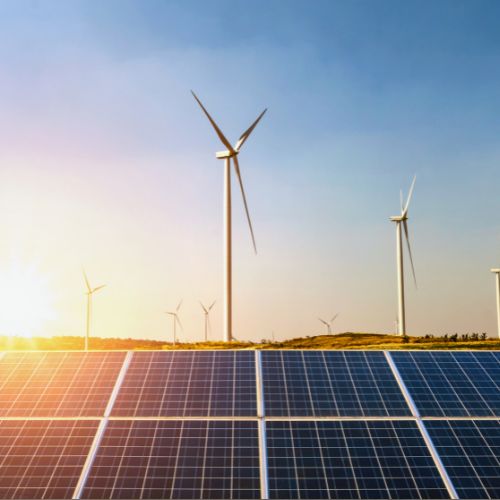
Die casting can produce parts with complex geometries, high strength, and corrosion resistance. In addition to its applications in the new energy and old energy fields, die casting is also widely used in the renewable energy field.
For example,
- it is used to manufacture the blades, cabins, and gearboxes of wind turbines;
- it is used to manufacture solar panels, solar trackers, and solar inverters;
- it is used to manufacture water turbines, generators, and gates;
- and it is used to manufacture geothermal generators, geothermal pipelines, and geothermal pumps.